1. Basic Working Principle of Yarn Winders and Winding Machines
Yarn winders and winding machines are two critical pieces of equipment widely used in the textile industry, primarily for winding yarn from the spinning process into yarn spools. While their operation slightly differs, their fundamental goal is the same: to wind yarn uniformly and efficiently while controlling the tension.
The winding process typically begins when yarn is fed into the winder from the feeding device. The winder, or spool, is driven by a motor that rotates, and as the spool rotates, yarn is gradually wound onto it. The diameter of the spool increases as the yarn is wound, and at this stage, it is necessary to stabilize the yarn’s transport through the yarn feeding device and control the tension. To ensure the quality of the winding, the motor speed of the winder, the speed of the yarn feeding motor, and the speed of the traverse mechanism need to be adjusted. This coordination helps prevent issues such as uneven yarn tension or improper winding.
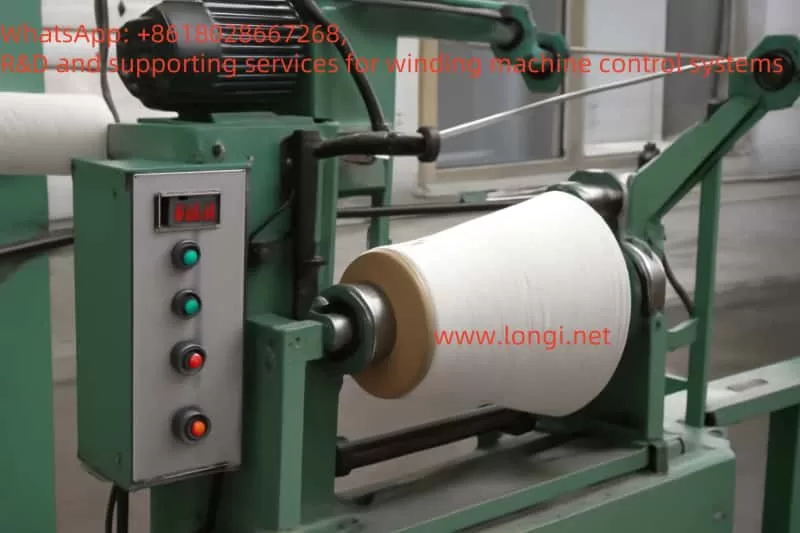
2. Core Parameter Calculation Methods
In the winding process, critical parameters such as yarn speed, yarn length, and tension directly affect the quality of the winding. To ensure an efficient and stable winding process, it is essential to accurately calculate and set these core parameters.
1. Calculation of Yarn Speed
Yarn speed refers to the linear speed at which the yarn moves through the winding device, typically measured in meters per minute (m/min). Yarn speed directly affects yarn tension and the efficiency of each winding cycle. The calculation formula is: Yarn speed(m/min)=Spool diameter(mm)×π×Chain speed(r/min)1000\text{Yarn speed} (m/min) = \frac{\text{Spool diameter} (mm) \times \pi \times \text{Chain speed} (r/min)}{1000}
Where the spool diameter (D) is the diameter of the yarn spool formed during the winding process, and the chain speed is the speed of the motor. The formula uses π\pi as the constant for calculating the circumference, and 1000 is the conversion factor from millimeters to meters. This formula allows for calculating the actual yarn speed during the winding process.
2. Calculation of Yarn Length
Yarn length refers to the total length of yarn used in each winding cycle. The formula for calculating yarn length is: Yarn length(m)=Yarn weight(g)×9000Yarn Denier(Den)\text{Yarn length} (m) = \frac{\text{Yarn weight} (g) \times 9000}{\text{Yarn Denier} (Den)}
Yarn denier is a unit of yarn density, representing the weight of 9000 meters of yarn. By knowing the yarn weight and denier, we can calculate the required winding length.
3. Tension Control
Tension is one of the most important parameters in the winding process. It directly determines the tightness and uniformity of the winding. Since the diameter of the spool changes during the winding process, yarn tension will fluctuate as well. Typically, when the spool diameter is small, the yarn tension is high, and when the spool diameter increases, the tension decreases.
To maintain stable tension, it is necessary to adjust the motor speeds of the winder and yarn feeder, and the traverse speed, which can effectively prevent the yarn from becoming too loose or too tight. The stability of tension is a key factor in the final yarn quality and affects properties such as yarn strength and elasticity.
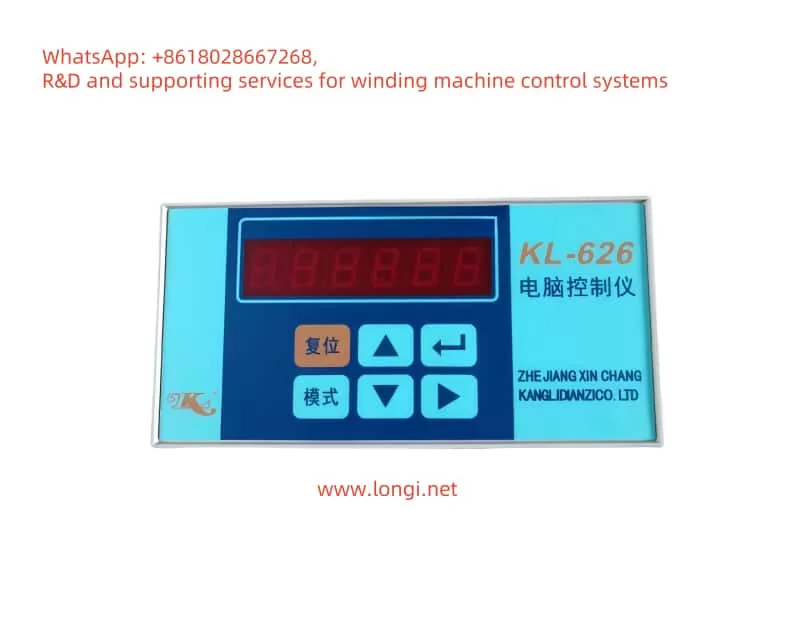
3. Key Points for Winding and Yarn Feeding Control
The control of winding and yarn feeding involves several factors, mainly coordinating the motor speeds of the winder, yarn feeder, and traverse mechanism to ensure uniform and orderly yarn placement.
- Winder Motor Control: The winder motor needs to adjust its speed to accommodate the increasing spool diameter. As more yarn is wound, the diameter of the spool increases, and the motor speed needs to decrease accordingly to ensure that the yarn tension does not become excessive. In this case, the sway frequency function can help adjust the frequency fluctuations, preventing tension fluctuations caused by a constant frequency.
- Yarn Feeder Motor Control: The primary task of the yarn feeder motor is to transport the yarn from the supply device to the winder. The speed of the yarn feeder needs to be coordinated with the winder motor speed to ensure that the yarn does not become too loose or too tight. The adjustment of the yarn feeder motor speed directly affects the stability of yarn transport.
- Traverse Mechanism Control: The traverse mechanism’s role is to adjust the yarn’s placement on the spool, ensuring each layer of yarn is laid down evenly. As the spool diameter changes, the traverse mechanism needs to adjust its speed according to preset parameters to maintain the correct yarn placement angle and density.
4. The Mechanism and Nature of Tension Stability
Tension stability is one of the most critical issues in the winding process, as any fluctuation in tension can lead to yarn breakage, slackness, or uneven winding. The stability of tension mainly relies on the following factors:
- Adjustment of Motor Speed: By adjusting the motor speeds of the winder and yarn feeder, the yarn tension can be kept uniform throughout the winding process. If the motor speed is too high, it may cause the yarn to become too tight; if it is too low, the yarn may become slack.
- Cooperation of the Traverse Mechanism: The control of the traverse mechanism helps to adjust the yarn’s tension distribution, especially when the spool diameter changes significantly. The traverse mechanism can balance the yarn’s tension in this case.
- Control of Frequency Fluctuations: As mentioned earlier, the sway frequency function adjusts the motor frequency periodically to stabilize tension and ensure that yarn remains uniform throughout the winding process.
- Real-Time Feedback and Adjustment: Although traditional winding control is mostly open-loop control, with the advancement of modern control technologies, many systems now integrate real-time monitoring and feedback mechanisms. By monitoring tension changes, the system can adjust motor speeds or traverse speeds to ensure tension remains within a preset range.
5. The Importance of Sway Frequency and Its Implementation
The sway frequency function is crucial in the winding process. By periodically adjusting the frequency fluctuations of the motor, it reduces and controls tension variations, preventing issues caused by frequent tension changes in the yarn. Modern frequency converters are generally equipped with this function, especially in the textile, spinning, and yarn winding industries. The sway frequency function has become an important method of controlling tension.
Implementation of sway frequency usually relies on the internal algorithms of modern frequency converters, which adjust the frequency periodically to simulate or adjust the mechanical motion during actual production, ultimately achieving the optimal tension distribution effect.
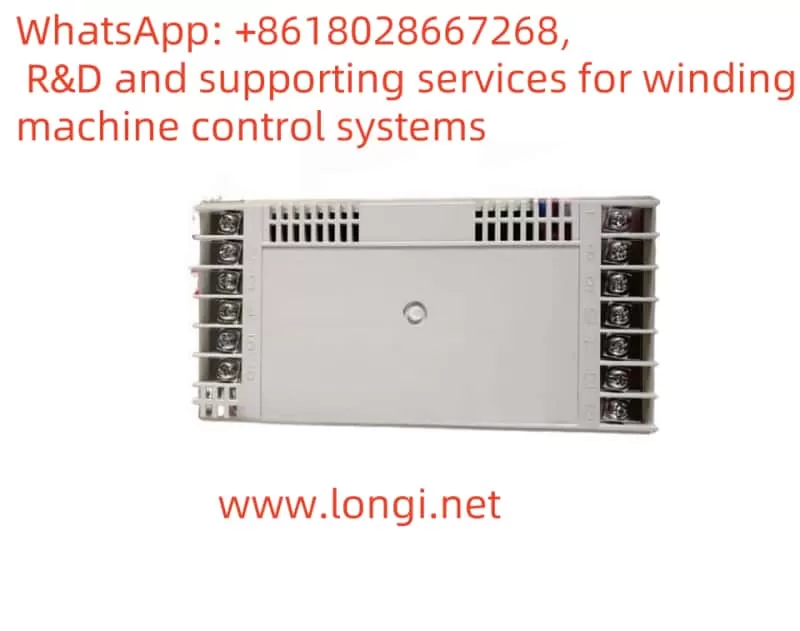
6. The Use of KL-626 Controller
The KL-626 controller is a commonly used device for yarn winders. Its primary function is to adjust the motor speeds, traverse motion, and tension control during the winding and yarn feeding process. The following are some key parameters and usage methods for the KL-626 controller:
- P.01DD Winding Mode: Used to select the winding mode, such as “Continuous”, “Shut-off”, etc. Different modes can be selected according to the production needs.
- P.02TR Running Time: Controls the running time for each cycle, i.e., the duration of each winding process. This needs to be adjusted according to actual needs.
- P.03L1 Starting Travel: Sets the starting position of the winder. It should be adjusted based on the length of the spool and the required number of winding layers.
- P.05F1 Starting Frequency: Sets the motor frequency at the start of the winding process. This parameter determines the initial yarn tension.
- P.07UT Traverse Speed: Controls the speed of the traverse mechanism. This parameter adjusts the speed at which the yarn is laid on the spool, based on the spool’s diameter and the required yarn placement density.
7. Replacement and Adjustment Ideas
With advancements in technology, modern frequency converters and PLC systems have gradually replaced some functions of the KL-626 controller. The sway frequency function in modern frequency converters can directly control the winder and yarn feeder motors, while the PLC can be programmed to achieve more flexible control. Here are some suggestions for replacement and adjustment:
- Using Modern Frequency Converters with Sway Frequency Function: Modern frequency converters with the sway frequency function can replace part of the KL-626 controller’s functions by adjusting the frequency fluctuations to stabilize yarn tension, simplifying the control system.
- Using PLC Control Systems: PLCs can programmatically control the frequency converter’s settings, adjust speeds, and monitor tension. PLCs offer higher flexibility and customizability, which makes them suitable for applications that require customized adjustments.
- Adjusting Key Parameters: Based on actual equipment requirements, key parameters like P.02 (running time), P.03 (starting travel), and others should be adjusted to ensure that tension is stable during the winding process, avoiding excess tightness or slackness.
8. Conclusion
The control of yarn winders and winding machines involves multiple critical parameters, with tension control being the most crucial. By optimizing the sway frequency function in modern frequency converters, adjusting motor speeds, and regulating traverse speeds, yarn tension can be stabilized during the entire winding process. The KL-626 controller, a traditional specialized controller, sets parameters to control the winding process, but modern frequency converters and PLC control systems have become important alternatives. With the help of these advanced control methods, the efficiency and quality of textile production have been significantly improved.