The Hilectro Hi2xx series servo drives are high-performance AC servo drives specifically designed for injection molding machines. This manual aims to provide users with a detailed operation guide, including product overview, safe operation, mechanical installation, electrical connection, parameter setting, troubleshooting, and more.
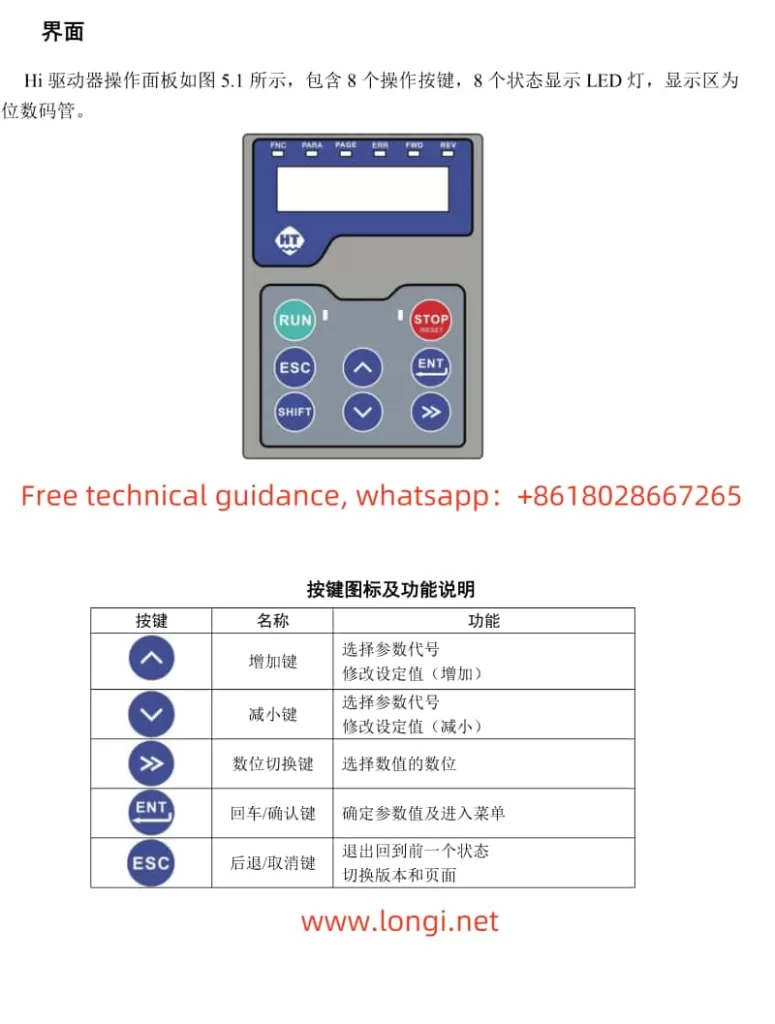
Product Overview
The Hilectro Hi2xx series servo drives are engineered to deliver precision control and high efficiency, making them ideal for the demanding applications of injection molding machines. These drives come with advanced features such as multiple communication protocols, rich I/O interfaces, and robust protection mechanisms to ensure reliable and stable operation.
Safety Precautions
General Safety Instructions:
- The drives contain voltages that can be lethal. Always ensure safe and correct operation to minimize risks to personal safety and equipment.
- During transportation, installation, and storage, prevent physical damage to the drives. Do not remove or bend the components and covers.
- Store the drives in their original packaging and avoid exposing them to humid, high-temperature environments or direct sunlight for prolonged periods.
Operational Safety:
- Before powering on, check that the power voltage matches the drive’s rated voltage, ensure correct wiring of inputs and outputs, and inspect for any short circuits. Always cover the drive before powering on.
- During operation, avoid touching the heat sink or discharge resistors. Non-technical personnel should not detect signals while the drive is running.
- After powering off, do not perform parameter storage operations as the capacitors may still hold high voltage for up to 5 minutes.
Mechanical Installation
Installation Environment:
- Choose an installation location with good ventilation and away from sources of heat, vibration, and dust.
Installation Space and Direction:
- Ensure adequate space around the drive for heat dissipation. Refer to the manual for specific spacing requirements based on the drive’s power rating.
- Install the drive vertically to facilitate heat dissipation. If multiple drives are installed, use a side-by-side arrangement.
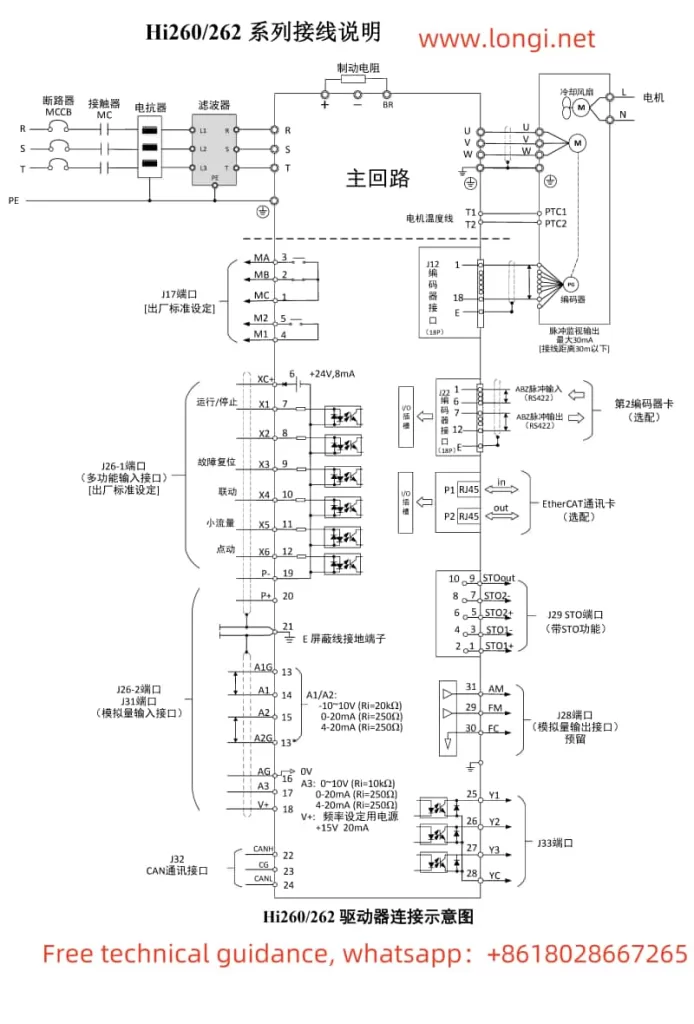
Electrical Connection
System Peripheral Connection:
- Connect the drive to the surrounding machinery using appropriate devices such as circuit breakers, contactors, input reactors, and filters to ensure safe and reliable operation.
Main Circuit Wiring:
- Refer to the wiring diagrams in the manual for connecting the main circuit terminals. Use the recommended copper wire size based on the drive’s power rating.
- Ensure that the grounding terminal (PE) is reliably grounded with a resistance value less than 10Ω.
Control Circuit Connection:
- Connect the control circuit wires according to the control board terminal layout. Pay attention to the signal levels and wiring requirements of each terminal.
Parameter Setting
The Hi2xx series servo drives provide a wide range of parameters for users to configure according to their specific needs. These parameters can be divided into several groups, such as Running Parameters (RU), Application Parameters (AP), Protection Parameters (PN), Motor Parameters (DR), etc.
Commonly Used Parameters:
- RU.01: Target Speed 1 (unit: r/min)
- AP.00: Command Source (e.g., 0: Terminal + Operator, 1: Terminal, 2: Bus)
- AP.01: Speed Command Source (e.g., 0: Local, 1: Analog Input 1, 2: Analog Input 2)
- PN.00: Motor Overload Protection Enable (0: Disable, 1: Enable)
- DR.02: Motor Rated Power (unit: kW)
To set these parameters, users can use the built-in operation panel or connect to the drive via a computer using communication interfaces such as CAN or EtherCAT.
Troubleshooting
The manual provides detailed descriptions and troubleshooting methods for common faults and warnings. For example:
Fault Code Er053 (Drive Undervoltage):
- Possible Causes: Input power voltage is too low or fluctuates greatly.
- Solutions: Check the input power voltage and ensure it meets the drive’s requirements. If the voltage fluctuates, consider adding a voltage stabilizer.
Warning Code 18 (Drive Undervoltage Warning):
- Solutions: Monitor the input power voltage and take necessary measures to stabilize it.
Conclusion
The Hilectro Hi2xx series servo drives offer advanced performance and flexibility, making them an excellent choice for injection molding machine applications. By following this user manual guide, users can safely and effectively install, configure, and troubleshoot these drives to achieve optimal performance. Always refer to the manual for detailed information and specifications when performing any operation on the drives.