I. Scheme Overview
This scheme aims to apply the Lianchuang High-Tech LC400E inverter to the unwinding and slitting machine. By precisely controlling the motor speed and torque, it achieves automation and efficient operation of core functions such as unwinding, cutting, and rewinding. The scheme covers motor function analysis, wiring methods, parameter settings, function realization, and auxiliary equipment selection to ensure the efficiency and stability of the unwinding and slitting machine’s production.
II. Analysis of the Unwinding and Slitting Machine Structure and Motor Configuration
Equipment Functions
The unwinding and slitting machine is used to cut wide rolls of materials into multiple narrow rolls. Its core functions include unwinding, cutting, and rewinding.
Motor Configuration
- Unwinding Motor: Controls the unwinding speed of the parent roll and requires constant tension to prevent material slack or breakage.
- Rewinding Motor: Controls the winding of narrow materials and requires tension adjustment according to the roll diameter (trapezoidal tension).
- Cutting Motor: Drives the cutting components and requires precise speed control.
Control Requirements
Tension control is the core requirement. It needs to achieve constant tension during unwinding and trapezoidal tension during rewinding through motor torque control.
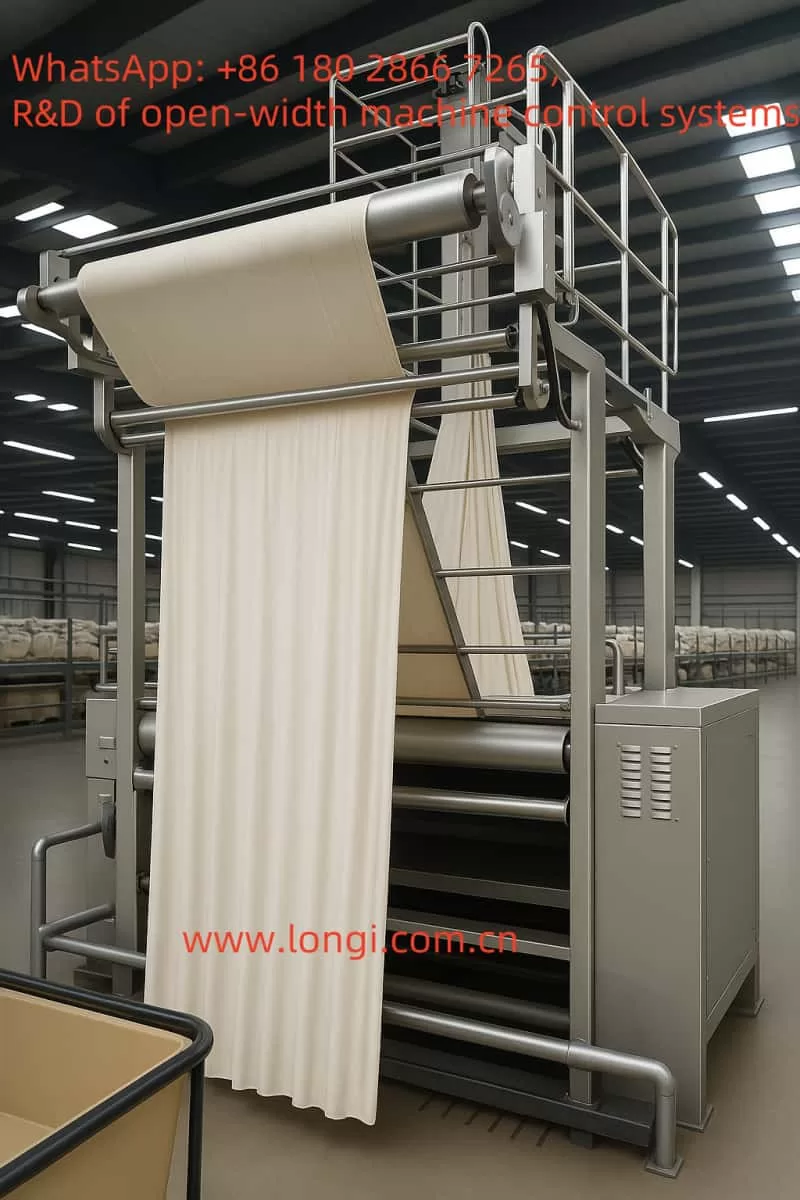
III. Key Features of the LC400E Inverter
- High-Performance Vector Control: Supports precise speed and torque control to meet tension synchronization requirements.
- Multi-Mode Control: Terminal control, analog input, and multi-speed settings to adapt to different working conditions.
- Safety Protection: Functions such as overvoltage, overcurrent, and motor protection ensure equipment safety.
- Communication Capabilities: Supports Modbus communication (RS232/RS485) for easy integration with PLC/HMI.
- Adjustable Parameters: Acceleration/deceleration time, PID control, and other parameters can be flexibly adjusted.
- Specifications: Power range from 0.75 kW to 500 kW, with output current reaching 63 A for models like G022/T4, suitable for the motor requirements of the unwinding and slitting machine.
IV. Application Positions of the LC400E in the Unwinding and Slitting Machine
- Unwinding Motor: Torque control mode to maintain constant tension.
- Rewinding Motor: Speed/torque control mode to support trapezoidal tension adjustment.
- Cutting Motor: Speed control mode to ensure cutting accuracy.
Application Suggestions: Configure multiple inverters according to the number of motors, such as one for the unwinding motor and one for the rewinding motor.
V. Wiring Methods
Main Circuit Wiring
- Connect the input terminals (R, S, T) to the three-phase power supply and the output terminals (U, V, W) to the motor. Connect the PE terminal to the ground.
- Refer to the LC400E manual for wire size specifications (e.g., for a 22 kW model, the input is 100 A, and the output is 63 A).
Control Circuit Wiring
- Start/Stop Control: DI1 (forward), DI2 (reverse), DI3 (stop).
- Speed Control: AI1 connects to the speed reference signal (e.g., potentiometer or PLC output).
- Tension Control: AI2 connects to the tension sensor output (if available).
- Fault Signal: DO1 connects to the alarm system.
- Communication: RS485 connects to the PLC/HMI.
Electrical Wiring Diagram (Text Description)
- [Main Circuit]
Power (three-phase) — R, S, T — LC400E — U, V, W — Motor
PE — Ground - [Control Circuit]
Start/Stop Buttons — DI1/DI2/DI3
Speed Reference — AI1
Tension Feedback — AI2
Fault Output — DO1
Communication — RS485 — PLC/HMI
VI. Parameter Settings
Basic Parameters
- P0-02: Set the operation command source to 1 (terminal control).
- P0-03: Set the frequency command source to 2 (AI1).
- P0-17/P0-18: Set the acceleration/deceleration time to 1.5 seconds.
- P6-10: Set the stop mode to 0 (deceleration stop).
Tension Control Parameters
- Unwinding Motor: Enable torque control (P3-00) and set the torque command source to AI2 (if a sensor is available).
- Rewinding Motor: Enable trapezoidal tension control (P7-00).
Multi-Speed Settings
- Set P0-03 to 6 (multi-speed command). Use DI4/DI5 to select the speed segment, and set the speed values in PC-00~PC-15.
Parameter Setting Table
Parameter Number | Function | Setting Value | Description |
---|---|---|---|
P0-02 | Operation Command Source | 1 | Terminal Control |
P0-03 | Frequency Command Source | 2/6 | AI1 or Multi-Speed |
P3-00 | Torque Control Mode | Enabled | Constant Tension During Unwinding |
P7-00 | Trapezoidal Tension Control | Enabled | Tension Adjustment During Rewinding |
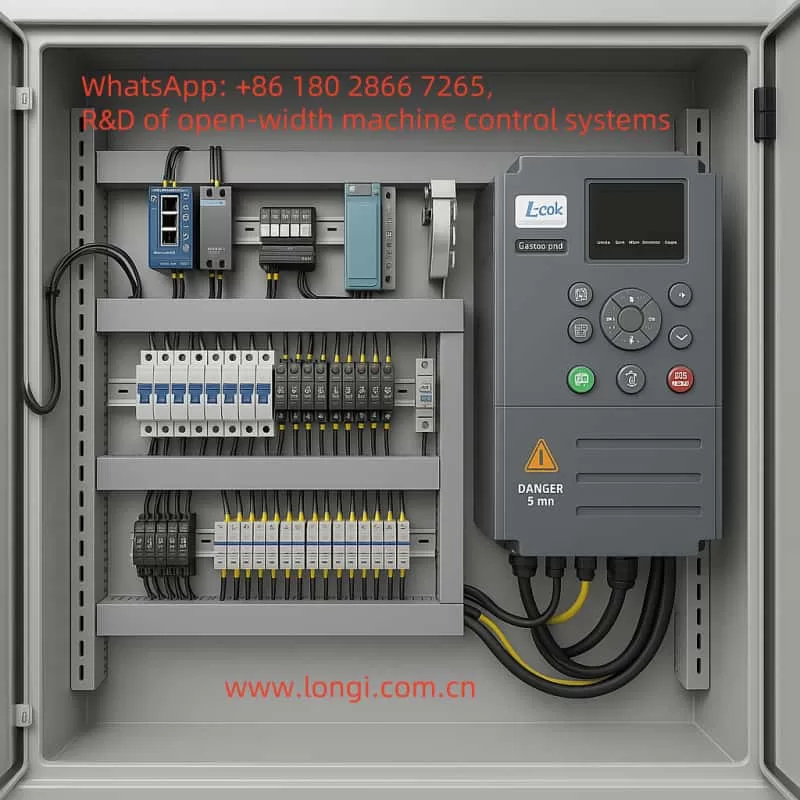
VII. Functions Realized
- Precise Speed Control: Set the speed through AI1 and support multi-speed switching.
- Tension Control: Maintain constant tension during unwinding and trapezoidal tension during rewinding to prevent material breakage or slack.
- Synchronization Control: The PLC coordinates the operation of multiple motors to ensure uniform tension.
- Fault Protection: DO1 outputs fault signals, and P6 group parameters set protection functions.
- Communication Integration: Modbus protocol enables remote monitoring and parameter adjustment.
VIII. PLC, Touch Screen, and Industrial Computer Selection
PLC Selection
- Recommended models: Siemens S7-1200 (high performance) or Mitsubishi FX series (cost-effective).
Touch Screen Selection
- Recommended models: Siemens KTP600 (easy to operate) or Mitsubishi GOT series (multi-language support).
Application Description
- PLC Functions: Read HMI inputs, send control commands, monitor status, and coordinate multiple motors.
- HMI Functions: Provide an operation interface, display status information, and support data logging.
Communication Connection
- Connect the PLC to the LC400E via RS485 with a baud rate of 9600 and no parity.
Control Diagram (Text Description)
- HMI — Ethernet/Serial — PLC
PLC — RS485 — LC400E (Unwinding/Rewinding/Other Motors)
PLC Program: Read HMI Inputs → Send Control Commands → Read Status → Update HMI Display
IX. Precautions and Safety Considerations
- Safety Protection: Install an emergency stop button and set inverter protection parameters.
- Tension Control: Prioritize the installation of tension sensors to ensure control accuracy.
- Multi-Motor Synchronization: Coordinate through the PLC to avoid uneven tension.
- Environmental Requirements: Install the inverter in a well-ventilated and dry environment, away from dust and moisture.
X. Summary
This scheme achieves high-precision speed and tension control through the application of the LC400E inverter in the unwinding and slitting machine, combined with PLC and HMI for automated operation. Key measures include:
- Adopting constant tension and trapezoidal tension control for the unwinding and rewinding motors, respectively.
- Using standard wiring methods and key parameter settings to ensure system stability.
- Selecting Siemens/Mitsubishi equipment to achieve efficient automated control.
This scheme can significantly improve the production efficiency of the unwinding and slitting machine, reduce operation difficulty and fault risks, and is suitable for the roll material processing industry.