1. Overview of the Fault
In industrial automation systems, the ABB ACS510 series VFD is commonly used to control the speed of 3-phase induction motors such as fans, pumps, and compressors. However, in some startup or operating conditions, users may encounter the following fault message on the control panel:
Display: F0022
Fault Type: SUPPLY PHASE (Phase Missing)
This fault is a protective response by the VFD, indicating an abnormality in the input power supply. According to ABB documentation and field service experience, F0022 means that the ripple voltage on the internal DC bus is too high—usually caused by a missing input phase or a blown input fuse.
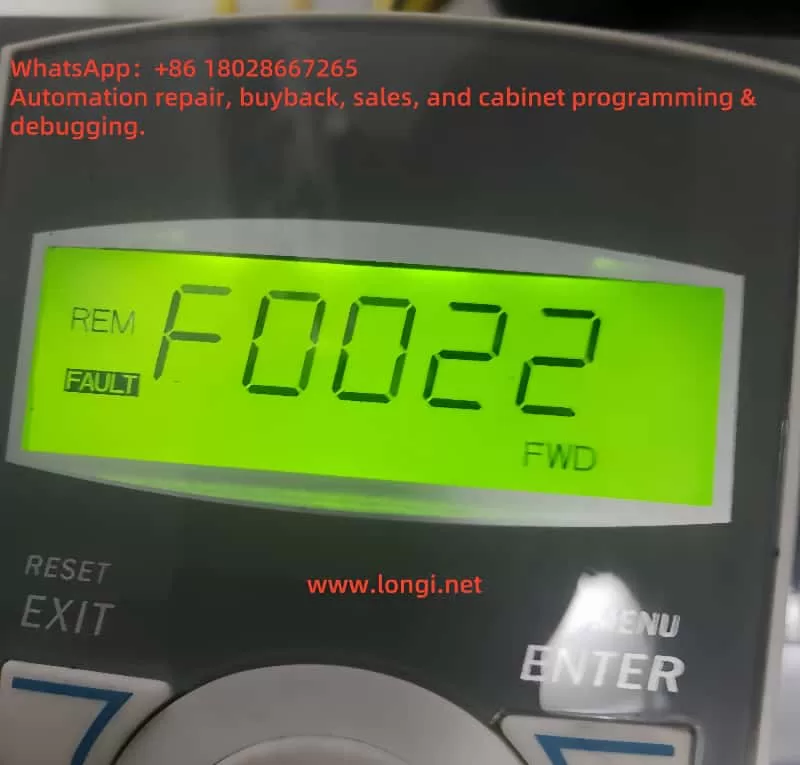
2. Root Cause Analysis of F0022
2.1 Nature of Supply Phase Missing
A 3-phase VFD relies on a stable three-phase AC input (U1-V1-W1) to convert into DC voltage through a rectifier bridge. If any one phase is lost or unbalanced, the resulting DC voltage will exhibit abnormal ripple levels.
⚠️ The ACS510 has internal monitoring circuits that detect high DC ripple voltage and trigger F0022 to protect the drive circuitry.
2.2 Common Causes
- Blown input fuse on one phase;
- Loose or oxidized input terminal connections;
- Wiring errors or damaged input cables;
- Phase loss due to upstream switchgear failure (e.g., contactors or circuit breakers);
- Severe voltage imbalance in the power supply;
- Non-simultaneous tripping of breakers causing a single-phase dropout.
3. Step-by-Step Troubleshooting for F0022
Follow these steps systematically to identify and fix the F0022 fault:
Step 1: Check for Actual Phase Loss
Use a multimeter or phase sequence meter to measure voltage between U1-V1-W1 on the drive input:
- All three phase-to-phase voltages should read within rated limits (typically 380V ±10%);
- Any phase showing zero or very low voltage confirms a missing phase.
Step 2: Inspect Fuses
Open the power distribution panel and:
- Check if one of the fuses is open/blown;
- Test with a multimeter for continuity across each fuse;
- Replace faulty fuses with the correct type and current rating.
Step 3: Check Terminal Connections
- Ensure the terminal screws at U1/V1/W1 are tight;
- Remove any oxidized or burned wires and reconnect properly;
- Verify copper wire strands are not damaged or frayed.
Step 4: Verify Upstream Circuit Breakers or Contactors
- Inspect whether one contact is worn or not engaging properly;
- Replace defective contactors or breakers as needed.
Step 5: Check for Voltage Imbalance
- Even if all phases are present, large voltage differences can trigger F0022;
- Measure all three phases—any deviation beyond 10% is problematic;
- If imbalance is observed, investigate upstream transformer or supply source.
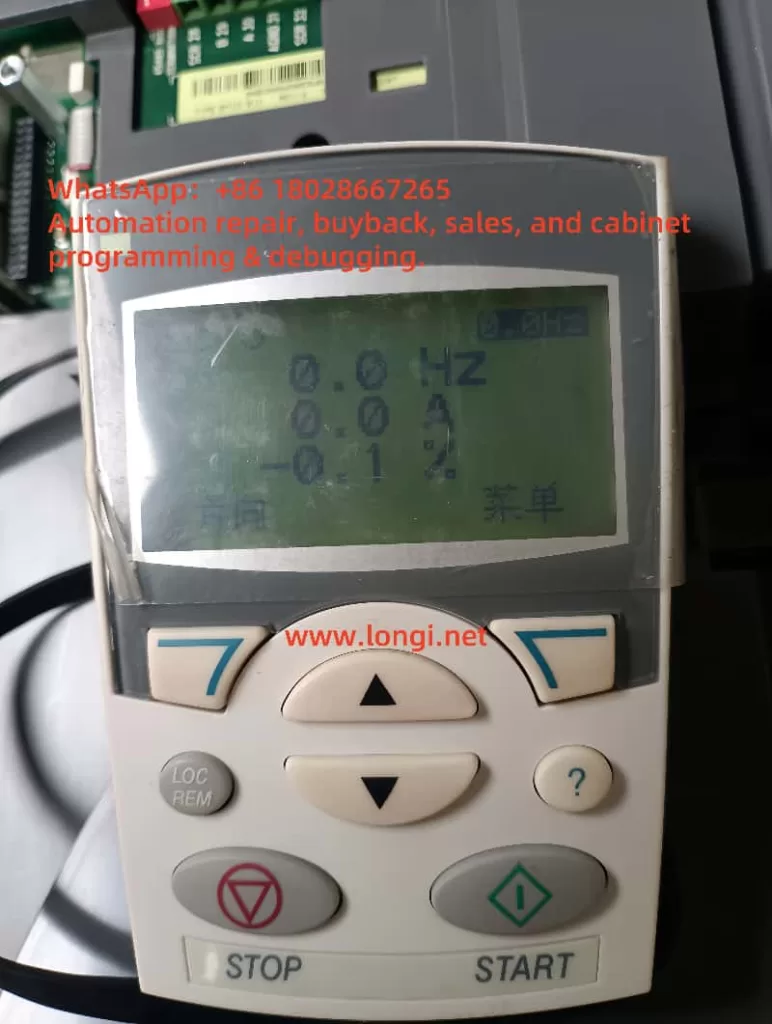
4. Preventive Measures for F0022
To prevent recurrence of this fault, consider the following strategies:
4.1 Use Proper Fuses and Breakers
- Use appropriately rated fuses with fast-acting response;
- Avoid low-quality circuit breakers with uneven trip behavior;
- All three phases should be protected with identical devices.
4.2 Add Phase Loss Protection Relay
Install a phase monitoring relay before the VFD input to shut down the system if a phase loss or imbalance is detected.
4.3 Perform Routine Terminal Maintenance
- Periodically check for loose or oxidized connections;
- Retorque terminal screws according to the drive’s manual;
- Re-terminate aged or discolored wires.
4.4 Stabilize the Power Supply
- Use voltage regulators if power quality is poor;
- For large-scale systems, consider using isolation transformers or UPS systems to ensure voltage stability.
5. Fault Reset and Drive Recovery
After eliminating the cause of the F0022 fault:
- Power down the drive and wait at least 5 minutes (for DC bus capacitors to discharge);
- Confirm that all input phases are present and balanced;
- Power on the drive and check if the fault is cleared;
- Press the RESET or STOP key to reset the fault;
- Resume normal operation as needed.
6. Conclusion
The F0022 “Supply Phase Missing” error in ABB ACS510 drives is a common input power issue indicating one or more phase anomalies. The built-in protection mechanism helps safeguard the VFD and motor from damage.
By understanding the electrical causes and following a structured diagnostic approach, maintenance personnel can quickly resolve this issue. Regular inspections, proper component selection, and proactive maintenance of power supply infrastructure are key to preventing such faults and ensuring stable long-term operation of the drive system.