In industrial automation, servo systems play a crucial role in precise control and efficient driving tasks. However, in practical applications, servo systems may encounter various faults that affect the stability and efficiency of production lines. One of the common error codes in the Inovance IS620P servo system is ER.258, which can disrupt the normal operation of the system. This article will provide an in-depth analysis of the ER.258 fault, explore its causes, and suggest reasonable handling methods.
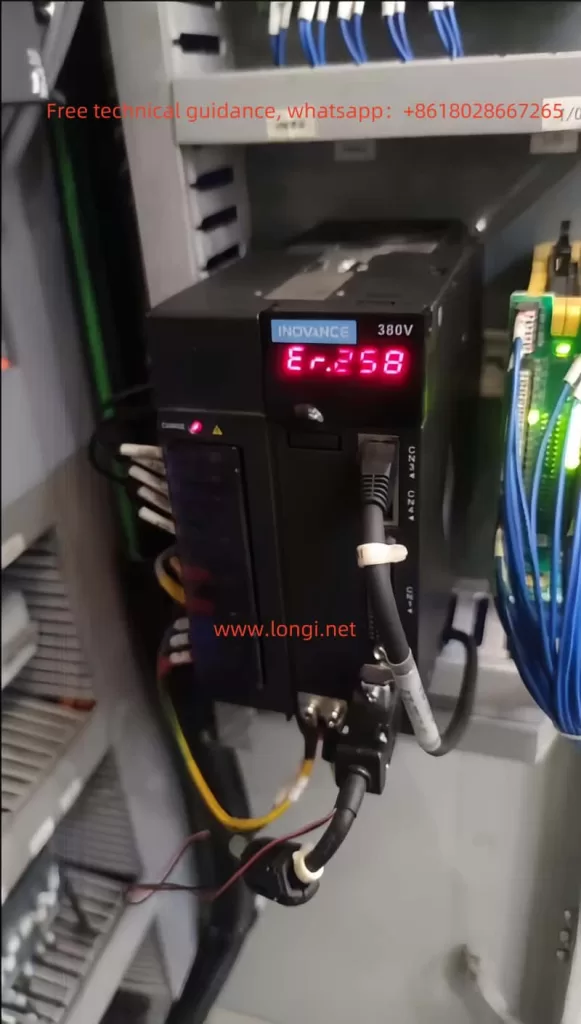
1. Analysis of ER.258 Fault
1.1 Basic Meaning of ER.258 Fault
The ER.258 fault is typically associated with the speed, torque, and position control in the servo system during the return-to-zero process. According to the design of the Inovance IS620P servo, the return-to-zero process begins after the motor contacts the limit switch. When the motor hits the limit switch, if the motor’s speed and torque meet certain threshold values, the system considers that the motor has reached the limit position and triggers the return-to-zero operation. However, in some cases, if the motor’s speed and torque are out of the normal range, or the system fails to accurately determine if the motor has stopped, the ER.258 fault is triggered.
1.2 Conditions for the Fault to Occur
Specifically, the ER.258 fault is triggered in the following situations:
- Overcurrent or Overload: When the motor contacts the limit switch, if the current suddenly increases, or if the resistance at the limit position is too high, causing the motor’s torque to exceed the allowed range, an overcurrent or overload protection alarm will be triggered.
- Exceeding Position Limit: When the motor reaches the mechanical limit, if it continues to try to move or cannot stop properly, the system considers that the motor has exceeded the predefined position and triggers the alarm.
- Motor Has Not Fully Stopped: When the H05-56 parameter is set too sensitively (such as setting it to 0), the system might wrongly interpret that the motor has stopped while it has not completely stopped, leading to the ER.258 fault.
1.3 Influence of H05-56 Parameter on the Fault
The H05-56 parameter plays an important role during the return-to-zero process. It sets the minimum speed threshold, and when the motor’s speed falls below this value, the system assumes that the motor has stopped and initiates the return-to-zero process. If H05-56 is set to 0, the system becomes overly sensitive in determining if the motor has stopped, which might lead to the motor not fully stopping, but the system falsely interpreting it as a stop and triggering the ER.258 fault.
1.4 Impact of Parameter Setting on the Fault
When the H05-56 parameter is set to 1, the system requires the motor’s speed to drop below 1 rpm before it determines that the motor has stopped and initiates the return-to-zero process. This provides more time and space for the motor to decelerate and avoids triggering the fault caused by speed instability or excessive torque. According to data, changes in the H05-56 parameter directly affect the system’s tolerance, ensuring that the motor and drive system will not cause overcurrent or excessive torque after contacting the limit switch, thus preventing the ER.258 fault.
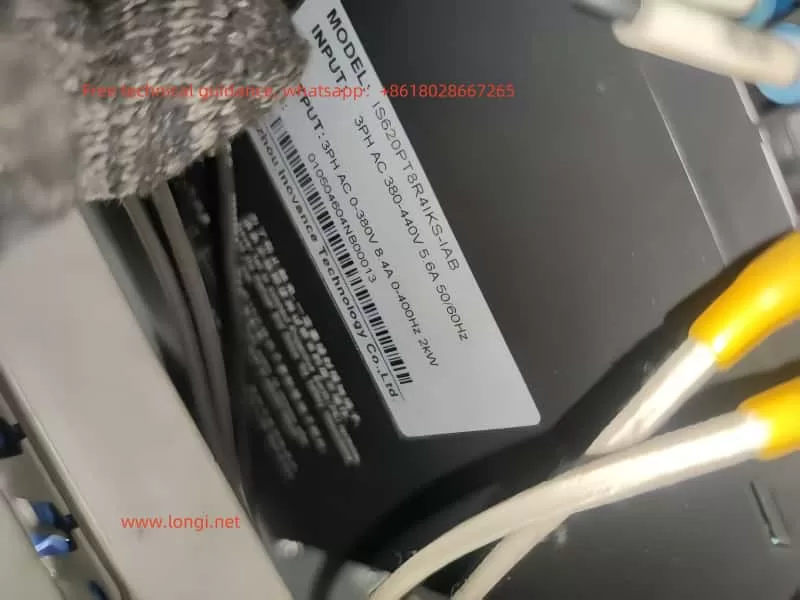
2. Causes of ER.258 Fault
2.1 Behavior of the Motor After Contacting the Limit Switch
During the return-to-zero process, the servo motor first contacts the mechanical limit switch. At this point, the motor’s torque and speed will be significantly affected. Once the motor contacts the limit switch, the system evaluates the motor’s speed and torque. If the torque exceeds a certain set value, the system assumes that the motor has reached the mechanical limit and stops further movement. If not, the motor may continue to attempt movement, leading to abnormal current or torque, triggering the ER.258 fault.
2.2 Incorrect Determination of Motor Stop Status
When the H05-56 parameter is set to 0, the system may mistakenly determine that the motor has stopped even if it has not completely stopped. This could happen because the motor might still have slight inertia or be moving slightly, causing the system to incorrectly interpret this as a stop condition and initiate the return-to-zero process prematurely, leading to the fault.
2.3 Excessive Current and Torque
After the motor contacts the limit switch, it may experience significant resistance or load, generating excessive torque. If the current exceeds the maximum allowable capacity of the drive, the system will trigger an overcurrent alarm, causing the ER.258 fault to occur.
2.4 Uneven Load or Slow Deceleration
If the motor’s load is uneven or the deceleration process is slow, the motor may continue to attempt movement after contacting the limit switch, generating excessive current or torque, triggering the ER.258 fault. Proper adjustment of the H05-56 parameter can help prevent this situation.
3. Handling Methods for ER.258 Fault
3.1 Adjusting the H05-56 Parameter
As mentioned earlier, the H05-56 parameter has a significant impact on the system during the return-to-zero process. Setting H05-56 to 1 can effectively prevent the ER.258 fault. This setting requires the motor’s speed to drop below 1 rpm before it is considered stopped, thus providing more time for the motor to decelerate and avoiding triggering the fault due to instability.
3.2 Checking Load and Torque
During the return-to-zero process, the motor’s load and torque can cause excessive current, triggering the ER.258 fault. Check whether the motor’s load and torque are too high and ensure that the motor can stop stably after contacting the limit switch. This will help avoid overcurrent or overload protection from being triggered.
3.3 Calibrating the Limit Switch
Check and calibrate the position of the mechanical limit switch to ensure that the motor stops at the correct position. Early or late contact with the limit switch could prevent the motor from stopping properly, leading to excessive torque and current, and triggering the ER.258 fault.
3.4 Adjusting the Motor’s Deceleration Settings
If the motor’s deceleration process is too slow, it may cause excessive torque or current, triggering the fault. Adjust the motor’s deceleration time and method to ensure that the motor decelerates smoothly after contacting the limit switch, avoiding excessive current and torque.
3.5 Regular Maintenance and Inspection
Regularly inspect the operation status of the servo system, including the motor, drive, limit switches, and other components. Clean the mechanical parts from dirt and check the motor’s operating condition to ensure that the system operates within normal ranges and prevent faults due to wear or malfunction.
4. Conclusion
The ER.258 fault is a common alarm in the Inovance IS620P servo system during the return-to-zero process. It is usually related to motor speed, torque, position control, and the functioning of the limit switch. By adjusting the H05-56 parameter, checking the load and torque, calibrating the limit switch, optimizing the motor deceleration settings, and performing regular maintenance, the occurrence of the ER.258 fault can be effectively prevented. Proper system settings and regular maintenance ensure the stable operation of the servo system, improving the reliability and efficiency of the equipment.