The KEB F5 series inverters are versatile and powerful devices used widely across industries for motor control and energy efficiency. This guide consolidates essential instructions and insights from various manuals to provide a comprehensive reference for daily operation, including starting, stopping, speed control, and troubleshooting.
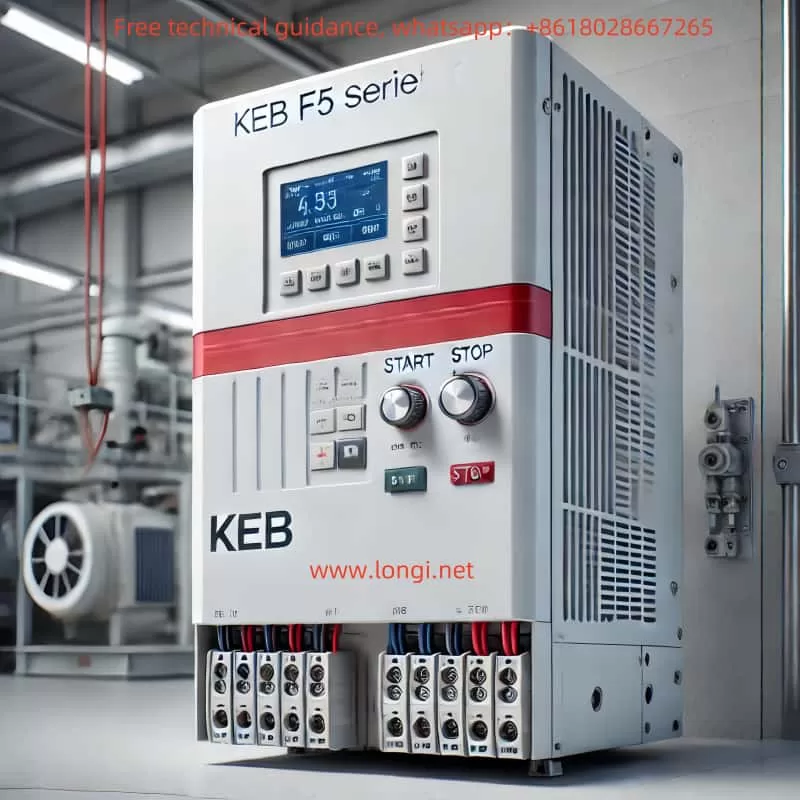
1. Overview of Common Usage Methods
1.1 Starting and Stopping the Inverter
To ensure safe and effective operation, follow these steps:
- Startup Procedure:
- Connect the power supply as per the wiring instructions in the manual.
- Ensure all safety interlocks and protective devices are active.
- Use the control panel or external start/stop commands to initiate the inverter.
- Check the display for proper status indications (e.g., “Run” mode).
- Stopping Procedure:
- Use the stop button on the control panel or external command inputs.
- Ensure the motor decelerates smoothly to prevent mechanical stress.
- Verify that the inverter returns to “Stop” mode on the display.
1.2 Speed Control and Parameter Adjustment
The F5 series supports flexible speed control via:
- Analog Inputs: Use a potentiometer or external signal to set the desired speed. Adjust parameters such as AN1 and AN2 for signal scaling.
- Digital Inputs: Configure fixed speeds via digital input terminals (e.g., X2A.10 and X2A.11) as per the CP parameters.
- Control Panel: Manually set speeds through the operation keypad by navigating to the appropriate menu.
- Ramp Settings: Configure acceleration and deceleration times (e.g., CP.20 and CP.21) to suit the application.
1.3 Protective Functions
The inverter includes several built-in protection mechanisms, such as:
- Overcurrent (E.OC)
- Overvoltage (E.OP)
- Overload (E.OL)
- Motor overtemperature (E.OH)
These features safeguard both the inverter and the connected motor, ensuring reliable operation.
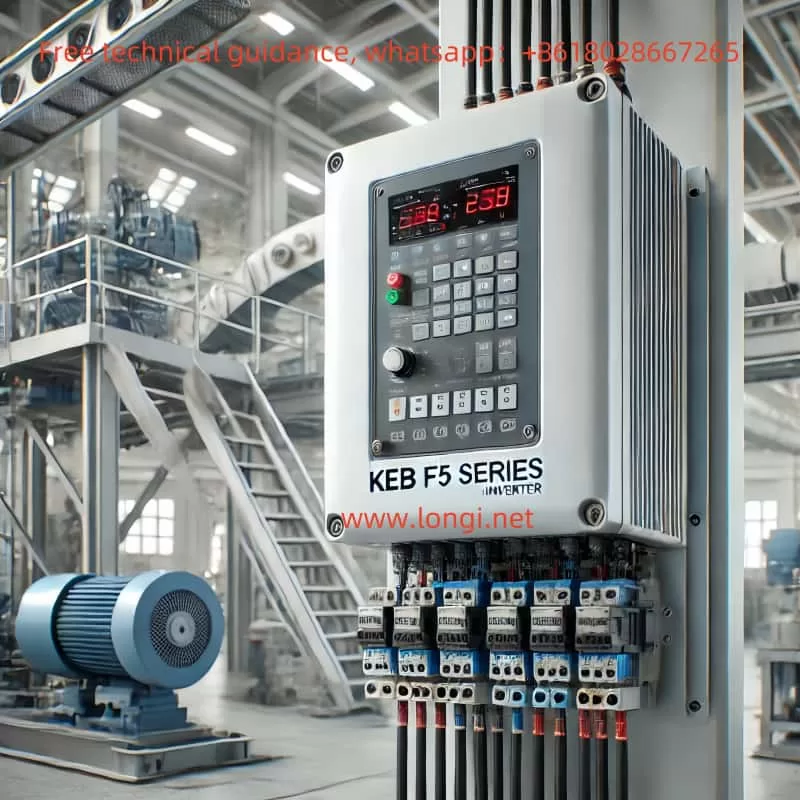
2. Troubleshooting Common Faults
The F5 series displays fault codes on the control panel to assist with diagnostics. Below are some frequently encountered errors and their solutions:
2.1 Fault Code List and Remedies
- E.OC (Overcurrent):
- Cause: Excessive load or short circuit in the motor.
- Solution: Check the motor connections and reduce the load if necessary. Inspect and replace damaged cables.
- E.OP (Overvoltage):
- Cause: Excessive regeneration energy from the motor.
- Solution: Increase deceleration time or add an external braking resistor.
- E.OL (Overload):
- Cause: Prolonged operation beyond the inverter’s capacity.
- Solution: Allow the inverter to cool and check motor power ratings.
- E.OH (Overheat):
- Cause: Inadequate cooling or excessive ambient temperature.
- Solution: Improve ventilation and clean cooling fans and filters.
2.2 Diagnostic Features
The “ru” parameter group provides real-time operating data:
- ru.0: Inverter status
- ru.1: Input frequency
- ru.2: Output frequency
- ru.18: DC bus voltage
- ru.39: Overload timer
Use these values to monitor performance and identify abnormalities.
3. Practical Tips for Optimal Performance
3.1 Parameter Group Adjustments
- Use the CP parameter group for configuration, covering essential settings like input/output scaling, motor control modes, and protection thresholds.
- Advanced users can access additional settings in the “In” and “Sy” groups for specialized applications.
3.2 Wiring and Installation Considerations
- Ensure proper grounding and shielded cables to minimize electromagnetic interference (EMI).
- Keep control cables and power cables separate to avoid cross-talk.
- Verify that terminal connections (e.g., X2A, X3A) match the manual’s specifications.
3.3 Regular Maintenance
- Inspect cooling fans, filters, and vents regularly to prevent overheating.
- Check all connections periodically for looseness or corrosion.
- Update firmware as recommended by KEB to ensure compatibility and reliability.
4. Recommended Applications and Limitations
4.1 Suitable Applications
The F5 series is ideal for:
- Industrial motor control (e.g., conveyors, pumps, fans).
- Precision speed and torque control.
- Energy savings in variable load applications.
4.2 Limitations
- Not designed for non-motor electrical loads.
- Requires proper environmental conditions (e.g., temperature, humidity) as specified in the manual.
Conclusion
The KEB F5 series inverters are versatile tools that offer reliable performance across diverse applications. By following this guide, users can achieve smooth operation, effective speed control, and swift resolution of common issues. For advanced settings or complex troubleshooting, refer to the detailed manual or consult KEB’s technical support.