I. Introduction to the Panel Functions and Operations of the Delta VFD-E Series Inverter
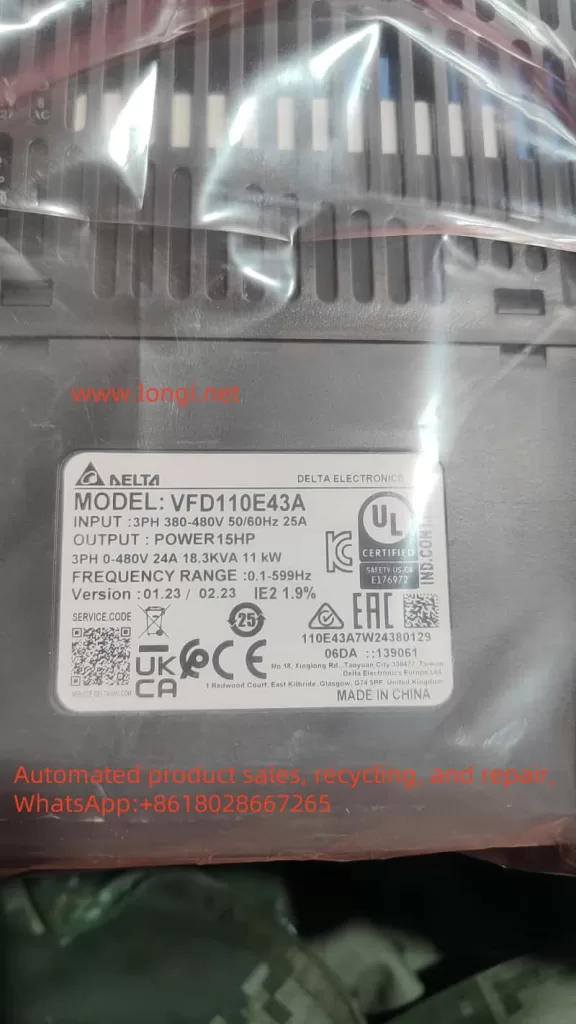
Panel Function Introduction
The panel of the Delta VFD-E series inverter primarily consists of the following function keys and display areas:
- Power Indicator: Indicates whether the inverter is powered on.
- RUN Indicator: Indicates the running status of the inverter.
- FREQ Display: Displays the current operating frequency of the inverter.
- MODE Key: Switches between different modes for parameter setting and monitoring.
- ▲/▼ Keys: Used for increasing or decreasing parameter values or frequency settings.
- STOP Key: Stops the operation of the inverter.
- RESET Key: Resets the inverter to its initial state or clears fault alarms.
- ENTER Key: Confirms the setting of parameters.
- JOG Key: Enables jogging (inching) operation of the motor.
- FWD/REV Keys: Controls the forward and reverse rotation of the motor.
Panel Operations
Copying Parameters to Another Inverter
- Connect to the Inverter: Use a suitable communication cable to connect the source inverter (containing the desired parameters) to the target inverter.
- Enter Copy Mode: On the source inverter, press the MODE key until the “Copy” mode is displayed.
- Initiate Copy: Press the ENTER key to initiate the parameter copy process.
- Complete Copy: Follow the prompts on the display to complete the parameter copy. Disconnect the communication cable after copying is finished.
Setting and Removing Passwords
Setting a Password:
- Navigate to the parameter group 00 User Parameters.
- Select parameter 00-08 Parameter Protection Password.
- Enter the desired password value (00-65535).
- Press ENTER to confirm.
Removing a Password:
- Navigate to the parameter group 00 User Parameters.
- Select parameter 00-08 Parameter Protection Password.
- Enter the password value you want to remove (set it to 00).
- Press ENTER to confirm.
Resetting to Factory Defaults
- Navigate to the parameter group 00 User Parameters.
- Select parameter 00-02 Parameter Reset Setting.
- Set the value to 09 for resetting to factory defaults at 50Hz, or 10 for resetting to factory defaults at 60Hz.
- Press ENTER to confirm and restart the inverter to apply the reset.
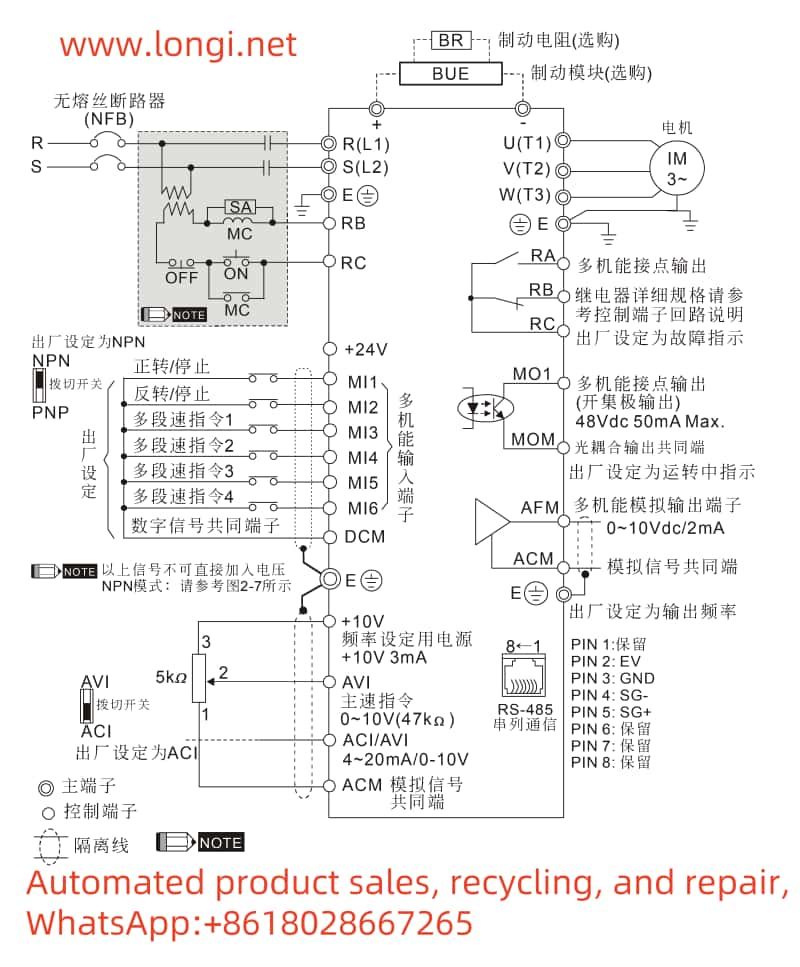
II. Terminal Control for Forward/Reverse Start and Stop
Terminal Control Configuration
- External Terminal Connection: Connect the external control terminals (FWD, REV, STOP) to the corresponding terminals on the inverter.
- Parameter Configuration:
- Navigate to the parameter group 02 Operation Mode Parameters.
- Set parameter 02-01 First Operation Command Source to 01 (External Terminal).
- Set parameter 02-05 Two-Wire/Three-Wire Control to the desired control mode (e.g., 00 for two-wire control).
- Control Logic:
- Forward Rotation: Close the FWD terminal and open the REV terminal.
- Reverse Rotation: Close the REV terminal and open the FWD terminal.
- Stop: Open both the FWD and REV terminals.
Monitoring and Troubleshooting
- Monitoring: Use the inverter panel or an external monitoring device to check the operating status and parameters.
- Troubleshooting: Refer to the inverter’s fault codes and troubleshooting guide in the user manual to diagnose and resolve issues.
By following the above steps, users can effectively operate and configure the Delta VFD-E series inverter for various applications, including terminal control for forward/reverse start and stop, parameter copying, password setting/removal, and resetting to factory defaults.