Principle and Features of the Instrument
The NETZSCH LF 467 series thermal conductivity analyzer uses the Laser Flash Method (LFA) to measure the thermal conductivity and diffusivity of materials. This method involves heating the front surface of a sample with a short energy pulse and measuring the resulting temperature change on the rear surface to calculate the thermal conductivity, specific heat, and thermal diffusivity【15†source】【21†source】. The basic formula is: λ(T)=a(T)⋅cp(T)⋅ρ(T)\lambda(T) = a(T) \cdot c_p(T) \cdot \rho(T)
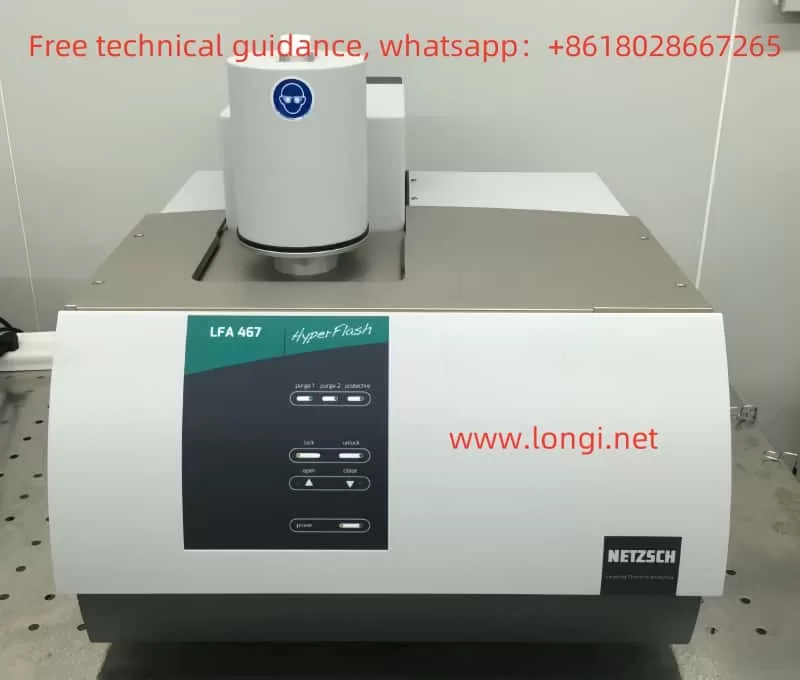
Where:
- λ\lambda: Thermal conductivity
- aa: Thermal diffusivity
- cpc_p: Specific heat capacity
- ρ\rho: Density
Key Features of the Instrument:
- Wide Temperature Range: Supports testing from -100°C to 1250°C, applicable to various materials【15†source】【19†source】.
- High Data Acquisition Rate: Up to 2 MHz, enabling precise testing of thin films and highly conductive materials【21†source】.
- ZoomOptics Technology: Optimizes the field of view via software-controlled adjustable lenses, avoiding signal distortion【17†source】【21†source】.
- Automation: Supports testing of up to 16 samples simultaneously, improving experimental efficiency【15†source】.
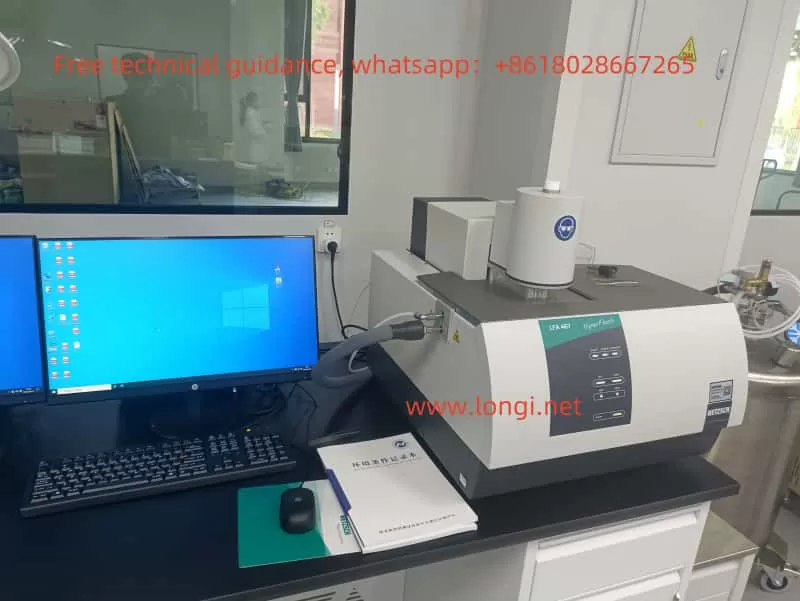
Operating Procedures and Precautions
Operating Steps:
- Prepare the Sample: Ensure the sample is flat and has a thickness between 0.1 mm and 6 mm. Measure the thickness and spray graphite on the sample surface to improve signal quality【15†source】【20†source】.
- Load the Sample: Open the furnace chamber, place the sample in the designated tray positions, record the positions, and close the chamber【20†source】.
- Set the Atmosphere: Choose an inert, oxidizing, or vacuum atmosphere as needed, and ensure the gas flow is properly adjusted【21†source】.
- Run the Experiment: Use the dedicated software to set testing parameters, such as laser pulse energy and acquisition time, and start the test while monitoring data in real-time【15†source】【20†source】.
- Analyze Data: Upon completion, the software automatically calculates thermal conductivity and diffusivity and generates a test report【21†source】.
Precautions:
- Ensure the furnace chamber is clean to avoid sample contamination or improper atmosphere.
- Avoid direct contact with the instrument during high-temperature operations and wear protective gear.
- Ensure the system is fully cooled before replacing cooling systems or adjusting gas flow【15†source】【20†source】.
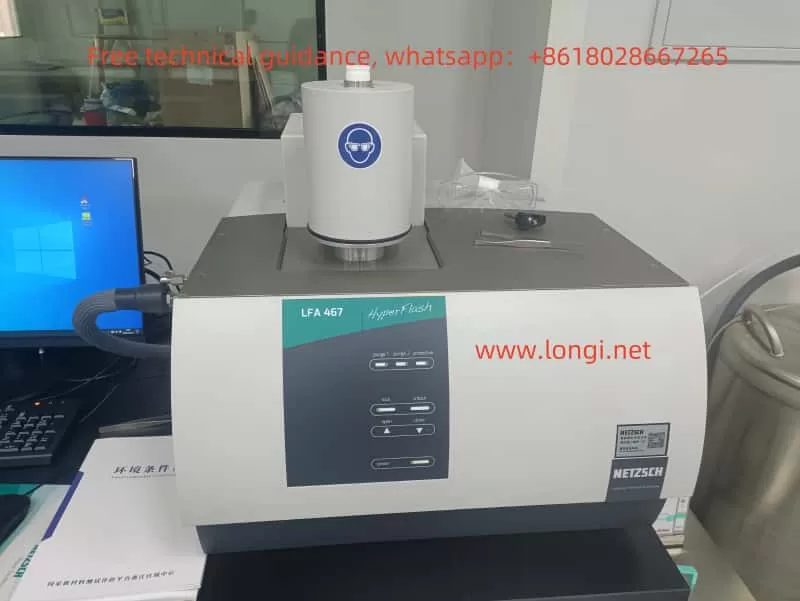
Fault Codes, Their Meaning, and Solutions
Fault codes for the NETZSCH LF 467 series analyzer are typically displayed in the software interface. Below are common issues and solutions:
- E001: Laser Source Failure
- Cause: Aging laser lamp or loose connection.
- Solution: Check the laser lamp connection; replace the lamp if necessary【15†source】.
- E002: Furnace Overheating
- Cause: Cooling system malfunction or furnace temperature control failure.
- Solution: Inspect the cooling system for adequate liquid levels and unobstructed pipelines; adjust the temperature controller settings【19†source】【21†source】.
- E003: Data Acquisition Failure
- Cause: Sensor malfunction or data acquisition card disconnection.
- Solution: Reconnect the data acquisition card and ensure the sensor connections are secure【20†source】.
- E004: Vacuum Pressure Abnormality
- Cause: Vacuum pump leakage or pressure sensor failure.
- Solution: Inspect the vacuum pump’s seals and recalibrate the pressure sensor【15†source】.
Conclusion
The NETZSCH LF 467 series thermal conductivity analyzer, with its efficiency, precision, and intelligent design, provides robust tools for studying the thermal properties of materials. By mastering its operation and troubleshooting techniques, users can significantly enhance experimental efficiency and ensure data reliability. Always operate according to the user manual’s guidelines to prolong the instrument’s lifespan and ensure testing safety.