1. Understanding the BLF Fault
The BLF (Brake Lift Failure) fault in Schneider ATV71 inverters is typically related to brake control logic. This fault indicates that the inverter has failed to reach the required current to release the brake. In other words, the inverter may not be triggering the brake release correctly, or the actual current is not reaching the preset release threshold.
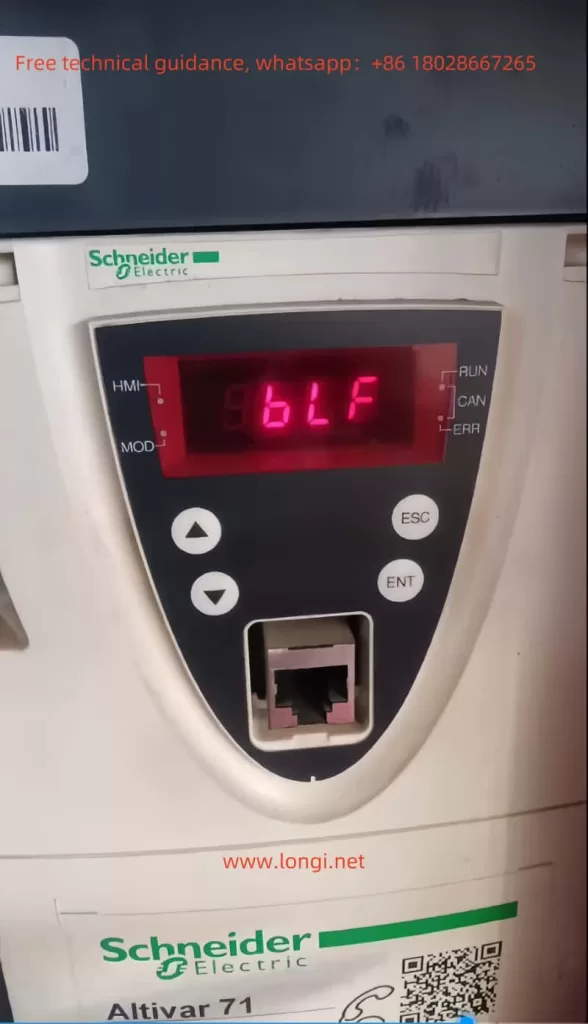
Possible causes of the BLF fault include:
- Incorrect brake connection: There may be wiring issues or poor contact between the motor and brake.
- Motor winding problems: Damaged motor windings could prevent the brake from being released properly.
- Improper parameter settings: The inverter’s brake release current or brake frequency threshold parameters (such as
Ibr
,Ird
,bEn
, etc.) may not be correctly configured. - Hardware failure: The brake relay, drive circuit, or the brake itself may be faulty.
2. Resolving the BLF Fault Through Parameter Adjustment
If the BLF fault is caused by incorrect parameter settings, follow these steps to adjust them:
- Check and adjust the brake release current parameters
- Access the inverter’s parameter settings and check
Ibr
(Brake Release Current – Forward) andIrd
(Brake Release Current – Reverse). - These parameters define the current required to release the brake. If set too low, the brake may not disengage properly. Adjust these parameters within the appropriate range (0 to 1.32 In).
- Access the inverter’s parameter settings and check
- Adjust the brake closing frequency
- The
bEn
(Brake Closing Frequency) parameter controls the frequency threshold at which the brake engages. Ensure this parameter is correctly set, preferably to Auto Mode or a manually defined frequency (0–10Hz).
- The
- Check the brake release time
- Extend the
brt
(Brake Release Time) if necessary to ensure the brake has enough time to disengage.
- Extend the
- Verify zero-speed brake control
- Ensure that
bECd
(Zero Speed Brake) is not mistakenly set toNo
, as this can affect the brake release logic.
- Ensure that
- Confirm the motor control type
- Go to the [Motor Control Type] (Ctt) parameter and ensure that the inverter’s control mode is appropriate for the motor and braking logic, especially for lifting applications.
3. Resolving BLF Faults Caused by Hardware Issues
If adjusting the parameters does not resolve the BLF fault, it may be caused by hardware failures. Follow these troubleshooting steps:
- Check motor and inverter connections
- Turn off the power and inspect the motor wiring to ensure proper connections and no loose terminals.
- Use a multimeter to measure the motor winding resistance to confirm there is no damage or short circuit.
- Inspect the brake relay
- Use a multimeter to check the relay contacts for proper switching and continuity.
- Check the brake solenoid
- If the motor uses an electromagnetic brake, verify that the brake is functioning correctly. Replace the brake coil if necessary.
- Examine the drive circuit
- If there is a problem with the control board, such as a faulty relay drive circuit, the inverter’s control board may need repair or replacement.
- Replace damaged components
- If any damaged components are identified, such as the brake system, control relays, or internal inverter parts, replace them accordingly.
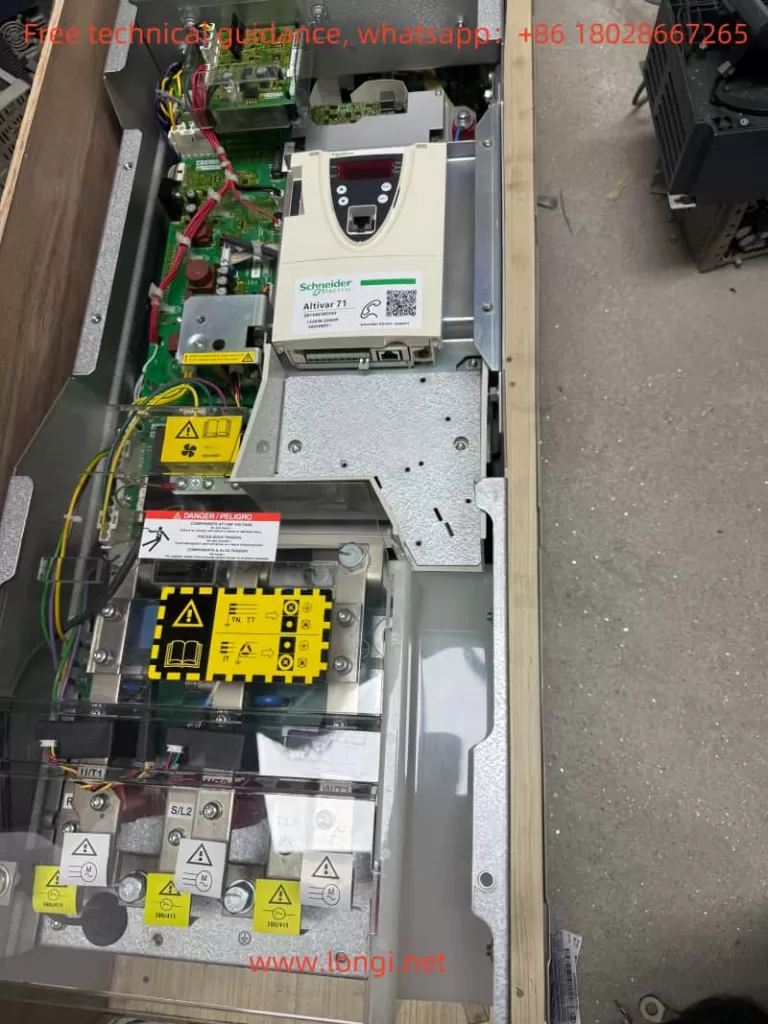
4. Conclusion
The BLF fault in Schneider ATV71 inverters is mainly related to brake control and may be caused by incorrect parameter settings or hardware malfunctions. Adjusting parameters such as Ibr
, Ird
, bEn
can resolve software-related issues, while hardware problems require thorough inspection of the motor, relays, brake system, and control circuits. A systematic troubleshooting approach will help pinpoint the root cause efficiently and ensure a proper repair solution.