In the realm of industrial machinery, inverters play a crucial role in converting direct current (DC) to alternating current (AC), enabling the efficient operation of various electrical devices. However, like any complex electronic system, they are susceptible to faults, especially after encountering events such as lightning strikes. This article delves into the diagnostic process and subsequent repair of a TECO 7200GA-30kW inverter that exhibited random shutdowns and starting difficulties following a lightning-related repair.
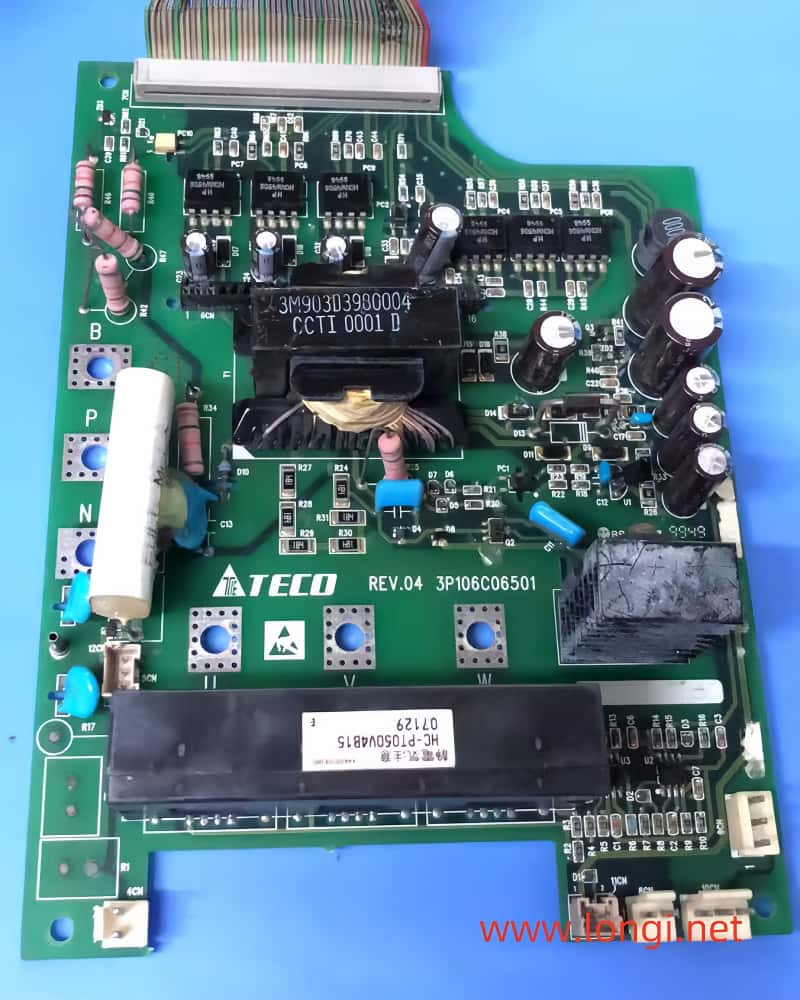
Initial Symptoms and Preliminary Inspections
The inverter, after being repaired from lightning damage, operated inconsistently for over a month. It experienced random shutdowns, sometimes occurring every few days or hours, and encountered difficulties during the starting process. Specifically, the capacitor charging short circuit contactor would jump, leading to failed starts, yet the operation panel did not display any fault codes. Despite these challenges, the inverter could occasionally start and run for a period before shutting down again.
To begin the diagnostic process, the control board was removed from the site. To bypass potential thermal protection issues, the terminals of the thermal relay were short-circuited. Similarly, the contact detection terminal of the capacitor charging contactor was short-circuited to prevent low voltage protection states. However, these measures did not resolve the issue, prompting a more comprehensive inspection. Upon detailed examination, no visible abnormalities were found, indicating that the problem was likely more complex and required a deeper investigation.
Identifying the Root Cause
With the control board reinstalled, testing revealed that the contactor jumped during startup, preventing the inverter from initiating. Interestingly, unplugging the 12CN plug cooling fan significantly improved the starting success rate. Observing the display panel during startup showed a decrease in brightness, suggesting a problem with the control power supply’s load capacity.
Further testing under load conditions revealed that while the power supply outputs were normal when unloaded, connecting resistive loads caused voltage drops. Specifically, when a 24V load was connected to the cooling fan and relay, the +5V line dropped to +4.7V. Although the screen display and other operations remained normal at this voltage, attempting to start the inverter resulted in the relay jumping and occasional fault codes such as “low DC voltage” and “communication interruption between CPU and operation panel.” Measurements indicated that when the +5V dropped below +4.5V, the inverter would automatically switch from the starting state to standby mode.
Analysis and Solution
The diagnosis of poor load capacity in the control power supply was confirmed. The CPU, with its strict power supply requirements, could barely function at voltages no less than 4.7V but would enter standby mode at voltages below 4.5V. The challenge lay in the fact that despite thorough checks, no components of the switch power supply were found to be damaged.
In an attempt to adjust the output voltage, a parallel resistance test was conducted on R1, one of the reference voltage divider resistors of the U1 (KA431AZ) voltage regulator. While this slightly increased the output voltage, the load capacity remained insufficient. Closer inspection of the circuit board revealed welding marks on the diversion adjustment tube Q1, indicating potential previous modifications. However, replacing Q1 with a similar component from another machine did not resolve the issue.
Given the complexity of the circuit and the high specificity of the transistors involved, particularly the bipolar transistor Q2 with high back pressure and amplification, a more nuanced approach was required. Analysis suggested that the working point of the shunt adjustment tube Q1 had shifted, causing excessive shunting of the base current of Q2. This, in turn, compromised the power supply’s load capacity.
To address this, a resistor (R6, 330 ohms) was series-connected with a voltage feedback optocoupler and a 47-ohm resistor. This modification aimed to reduce the base current of Q1, thereby decreasing its shunting capability towards Q2 and enhancing the power supply’s load capacity. Upon testing, the +5V line stably maintained 5V output, both under load and during startup operations, effectively resolving the issue.
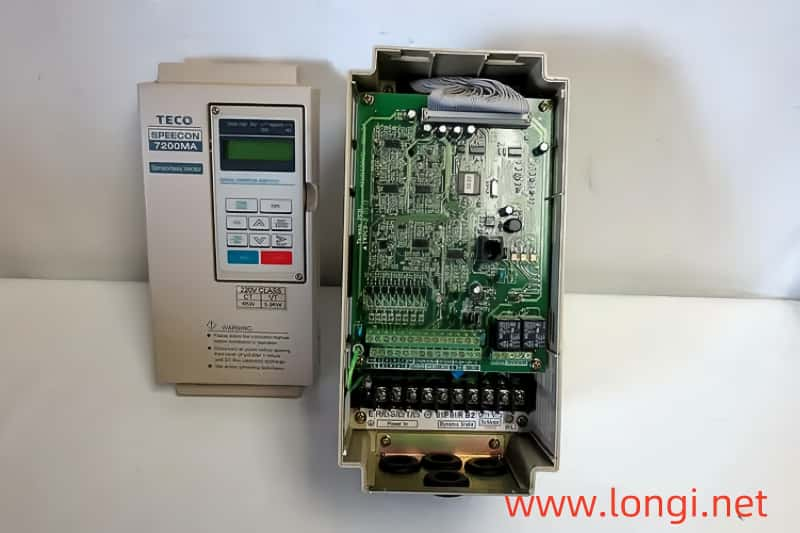
Fault Inference and Conclusion
The fault was inferred to be due to the aging of the Q1 switch tube, leading to a decrease in its amplification ability. This resulted in insufficient base current (Ib) after shunting, causing Q1 to become fully conductive and increasing its conduction resistance. Additionally, a characteristic deviation in the shunt branch led to excessive shunting and poor driving of the switching tube, further reducing the power supply’s load capacity.
In summary, the repair process of the TECO 7200GA-30kW inverter involved meticulous diagnostic steps, from initial symptom observation to component testing and eventual circuit modification. The successful resolution highlights the importance of understanding the intricate workings of electronic systems and the creative application of engineering principles to overcome unexpected challenges. This case study serves as a valuable resource for technicians and engineers facing similar issues in industrial electronics repair.