Introduction
When using ABB’s ACS series inverters, including ACS180, ACS530, ACS580, and ACS880, users may encounter the FAULT 7086 alarm code, which is not explicitly mentioned in the manuals for these models. This article delves into the reasons behind this alarm and provides comprehensive solutions to help users quickly identify and resolve the issue.
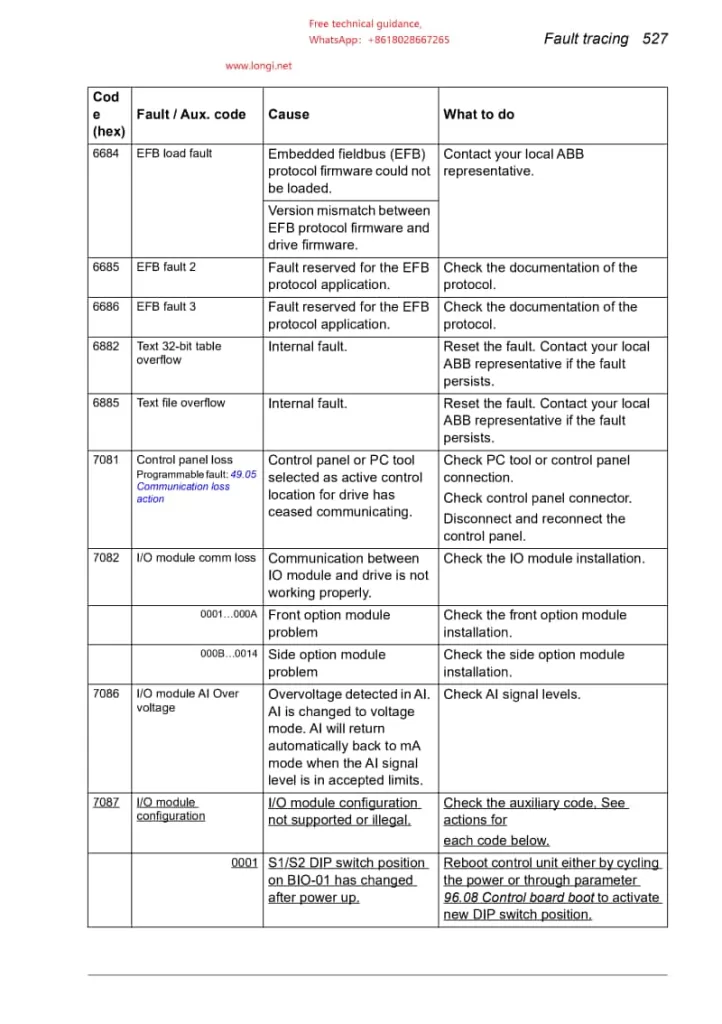
Background of FAULT 7086 Alarm
Although the operation manuals for ACS180, ACS530, ACS580, and ACS880 do not directly mention FAULT 7086, the explanation for this alarm code is found in the ACS380 (specifically designed for crane applications) manual. FAULT 7086 indicates “AI Overvoltage in I/O Module,” meaning that an overvoltage has been detected at the analog input (AI) port.
Cause Analysis
AI Port Overvoltage: When the input voltage at the AI port exceeds the set upper limit (typically 10VDC or a configurable value such as 7.5VDC), the inverter triggers the FAULT 7086 alarm to protect internal circuits from damage.
AI Signal Mode Change: If the AI signal level exceeds the acceptable range, the inverter may attempt to automatically switch the AI to voltage mode. If this fails, it will trigger the alarm.
Circuit Board Component Issues: Although the circuit board designs of ACS180, ACS530, ACS580, and ACS880 differ, they share a core control system. Issues with the mainboard, drive board connections, or related components can also lead to unexpected FAULT 7086 alarms.
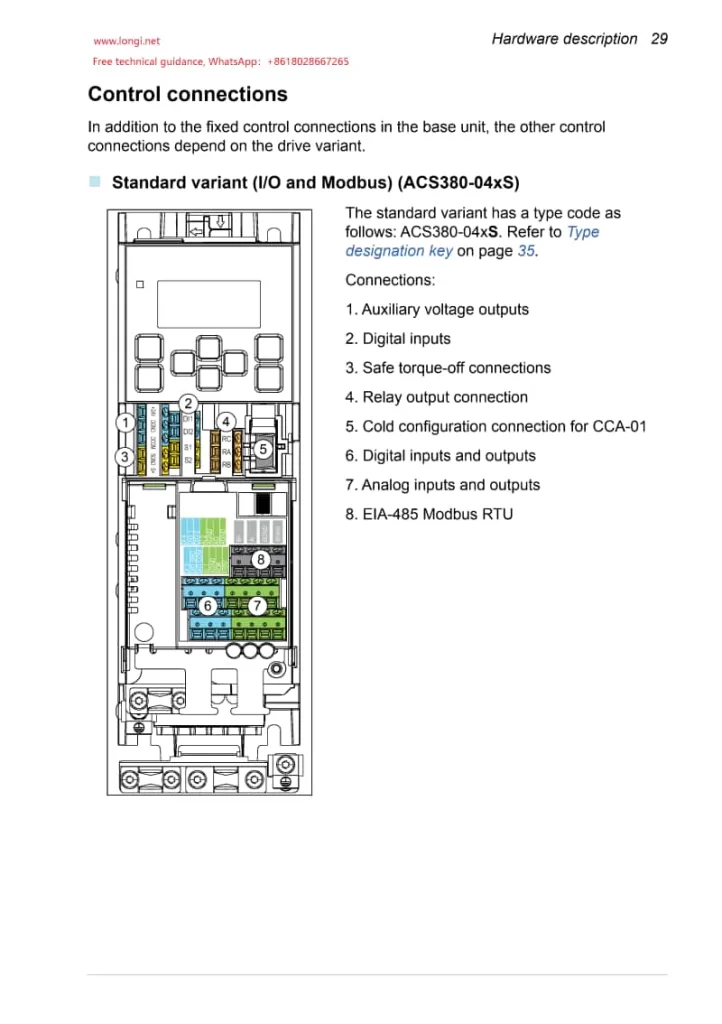
Solutions
1.Check AI Voltage:
(1)Use a multimeter to measure the actual input voltage at the AI port and confirm if it exceeds the set upper limit.
(2)Adjust the AI port’s voltage upper limit setting, if necessary, to suit the current operating 2.environment.
(1)Inspect External Connections:
Verify that the external signal source for the AI port is normal, with no abnormal fluctuations or damage.
(2)Check the connection cables and plugs for the AI port to ensure they are securely connected and free from looseness.
3.Examine Circuit Boards and Modules:
(1)If suspecting a circuit board or module failure, first inspect the cables and plugs between the mainboard and drive board, cleaning dust and ensuring good contact.
(2)If possible, try replacing suspected circuit boards or modules to verify if the issue is resolved.
4.Refer to Relevant Documentation:
(1)Although the ACS180, ACS530, ACS580, and ACS880 manuals do not directly mention FAULT 7086, refer to the ACS380 manual for more information on handling AI overvoltage.
(2)Contact our technical team for free technical consultation and assistance
5.Reset the Inverter:
After ruling out external hardware issues, attempt to reset the inverter to see if the alarm clears.
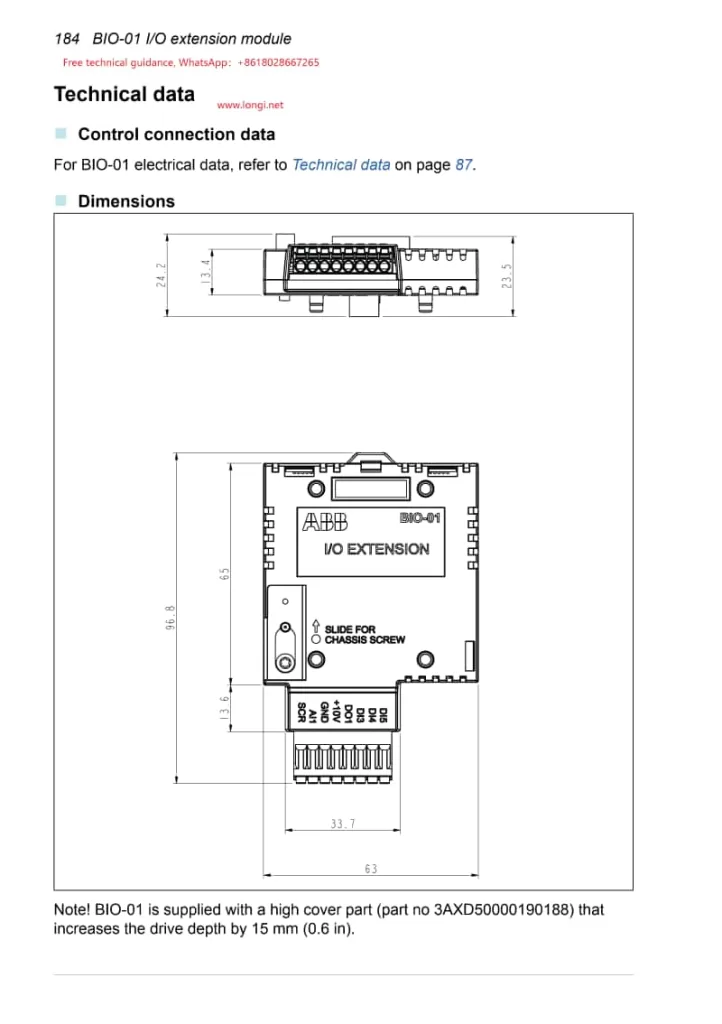
Conclusion
The FAULT 7086 alarm in ACS series inverters, including ACS180, ACS530, ACS580, and ACS880, can occur under specific circumstances not directly mentioned in their manuals. By thoroughly analyzing the alarm’s background and causes, and implementing appropriate solutions, users can effectively identify and resolve the issue. During the process, ensure safe operation and back up important data to prevent unexpected losses.