Thermal Conductivity Instruments (Including Laser Thermal Conductivity Tester, Flash Thermal Conductivity Tester, Thermal Reflectance Thermal Conductivity Tester, Thermal Conductivity Coefficient Tester, etc.) Play a Vital Role in Material Research and Testing, But May Encounter Various Faults During Use. Below Are Some Common Fault Scenarios and Corresponding Repair Methods:
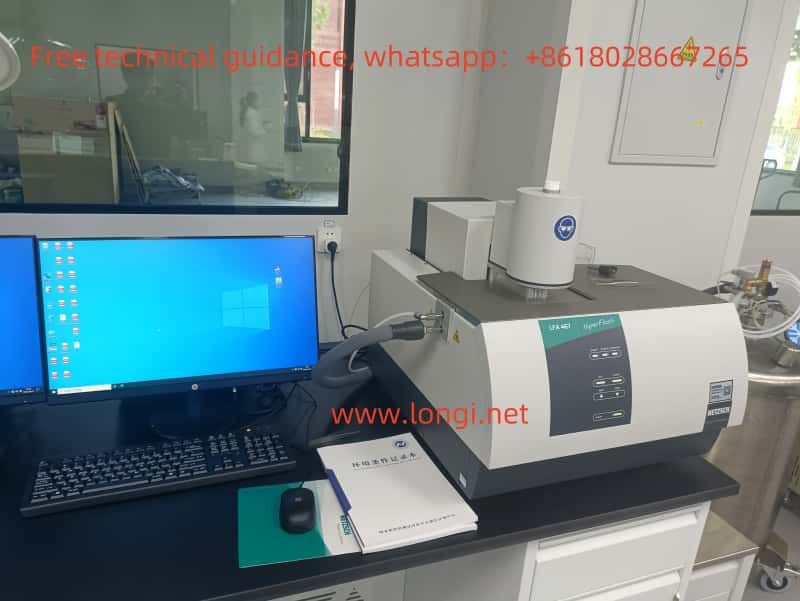
I. Common Fault Scenarios
1. Unstable Readings or Display Errors
- Possible Causes: Connection issues, sensor contamination, incorrect sample installation, unstable environmental conditions (e.g., temperature and humidity fluctuations).
- Repair Methods: Check and reconnect the device, clean the sensor, ensure correct sample installation, and stabilize environmental conditions.
2. Readings Too High or Too Low
- Possible Causes: Poor thermal contact, incorrect input of sample thickness or dimensions, instrument not properly calibrated.
- Repair Methods: Ensure good thermal contact between the sample and sensor, verify and correctly input sample parameters, and calibrate according to the manufacturer’s guidelines.
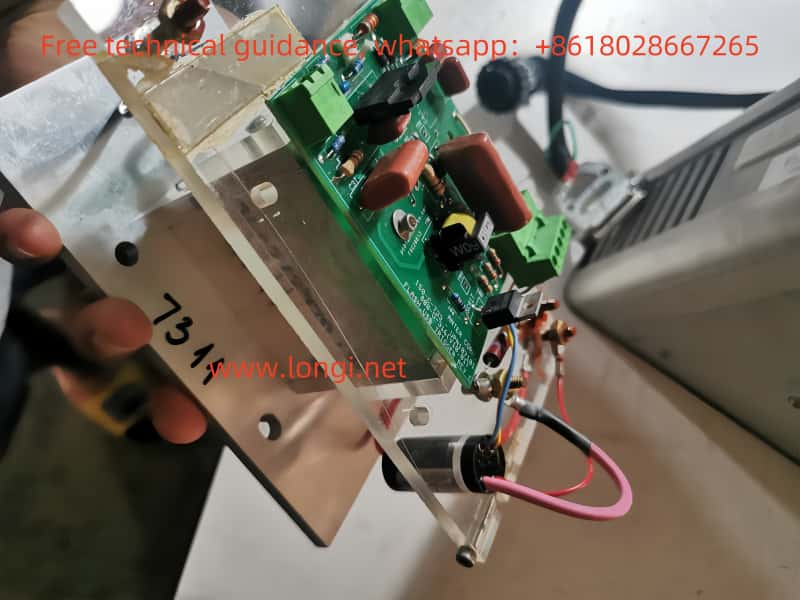
3. Slow Heating or Cooling Rates
- Possible Causes: Faulty heating or cooling elements, improper power and control settings, maintenance required.
- Repair Methods: Check the working status of heating or cooling elements, adjust power and control settings, and perform necessary cleaning or replacement of parts.
4. Readings Affected by External Interference
- Possible Causes: Electromagnetic interference, vibration, light interference.
- Repair Methods: Place the instrument in a light-shielded, vibration-free, and low-electromagnetic interference environment, and use shielding materials or isolation measures to reduce interference.
5. Software Operation Difficulties
- Possible Causes: Unfamiliarity with software functions, improper operation.
- Repair Methods: Thoroughly read the user manual or operation guide, contact Longi Ectromechanical Company for technical support, and attend training courses to improve operational skills.
6. Hardware Faults
- Possible Scenarios: Switch knob not fully rotated, copper wire desoldered, battery box wire broken, circuit board failure, laser head not emitting light, etc.
- Repair Methods: Inspect the hardware components such as switch knobs, copper wire soldering, battery box wires, and circuit boards, and repair or replace as necessary.
7. Light Source or Detector Faults
- Possible Causes: Unstable light source intensity, damaged detector.
- Repair Methods: Regularly check the working status of the light source and detector, and replace promptly if issues are found.
8. Data Acquisition System Faults
- Possible Causes: Hardware or software faults in the data acquisition system.
- Repair Methods: Check the working status of the data acquisition system and repair or replace if necessary.
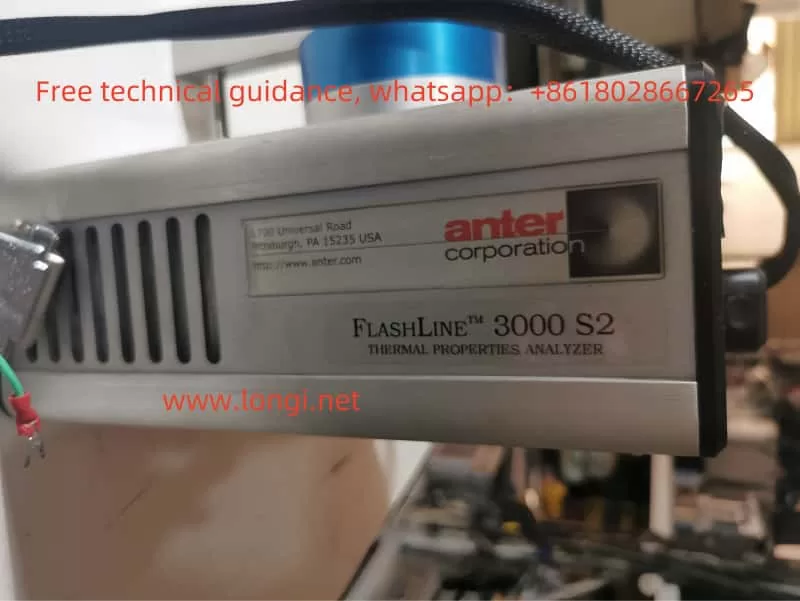
II. Repair Method Summary
Basic Checks:
- Inspect device connections, power supply, sensors, and sample installation.
- Ensure stable environmental conditions (e.g., temperature and humidity).
Calibration & Adjustment:
- Regularly calibrate the instrument following the manufacturer’s guidelines.
- Adjust instrument settings to ensure correct measurement parameters.
Hardware Maintenance:
- Clean sensors, heating or cooling elements, and other critical components.
- Inspect and repair or replace damaged hardware, such as copper wires, wires, and circuit boards.
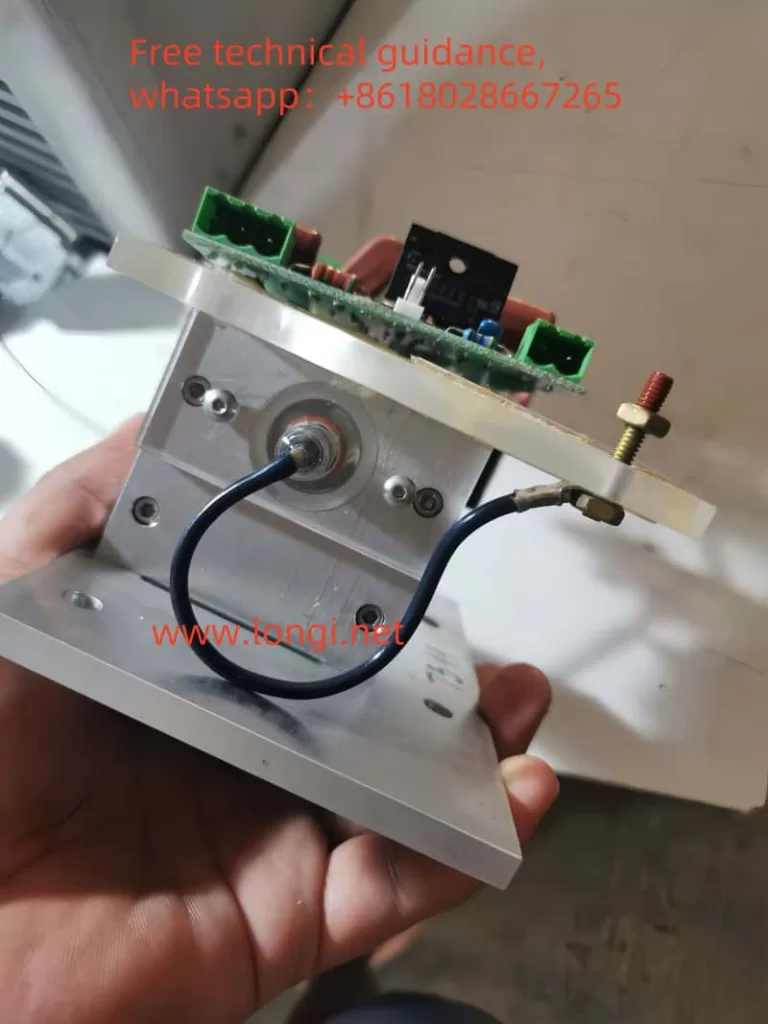
Software & Operation:
- Thoroughly read user manuals and operation guides to ensure correct software operation.
- Contact the manufacturer or technical support for assistance if needed.
Preventive Maintenance:
- Regularly inspect the working status of all device components and perform necessary maintenance and replacements.
- Establish maintenance records to track the usage status and repair history of the equipment.
Environmental Control:
- Ensure the device operates under stable environmental conditions and avoid external interference.
By implementing these repair methods, the accuracy and reliability of thermal conductivity instruments in material research and testing can be ensured, improving the precision of measurement data.
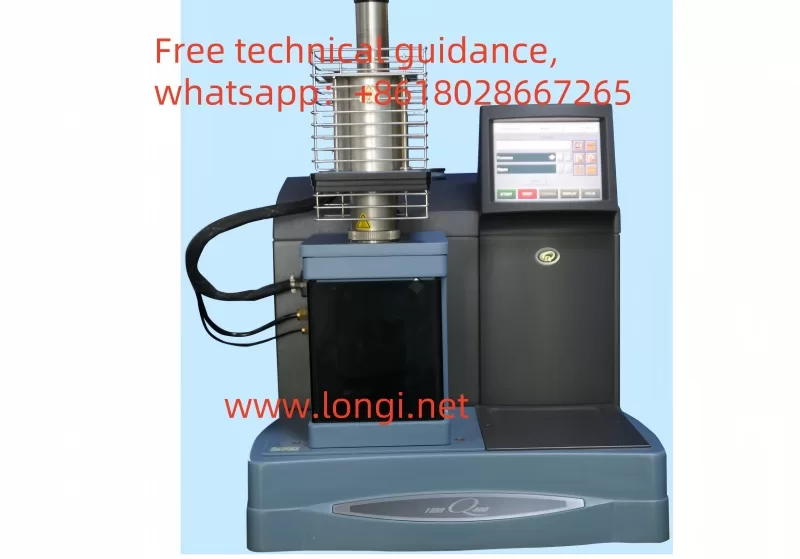
III. Brands and Models of Thermal Conductivity Instruments Repaired by Longi Ectromechanical Company
- NETZSCH (Germany)
- LFA467HT (LFA 467 HyperFlash)
- LFA 447 NanoFlash
- LFA 457 MicroFlash
- TA Instruments (USA)
- DLF1200
- DLF1600
- DLF2800
- Linseis Thermal Analysis (Germany)
- LFA1000
- LFA500
- Thermophysical Instruments (Japan)
- TC1200
- TC7000
- C-Therm Technologies (Canada)
- TCi Thermal Conductivity Analyzer
- Trident Thermal Conductivity Analyzer
- KEM (Japan), Quick Thermal Conductivity Tester
- QTM-500
- QTM-710
- QTM-700
- TPS2500S
- Xiangtan Xiangyi Instrument (China)
- LFA 4000
- LFA 2000
- DRH-300
- DRH-ZD-300
- DRH-400
- DRH-ZD-400
- DRH-600
- DRH-ZD-600
- DRE-2A
- DRE-2B
- DRE-2C
- DRE-2D
- DRE-2E
- DRE-2D (duplicated, possibly an error)
- DRE-2G
- Phoenix Laser Thermal Conductivity Instruments (China)
- CORE EU
- Hangtian Ruibo
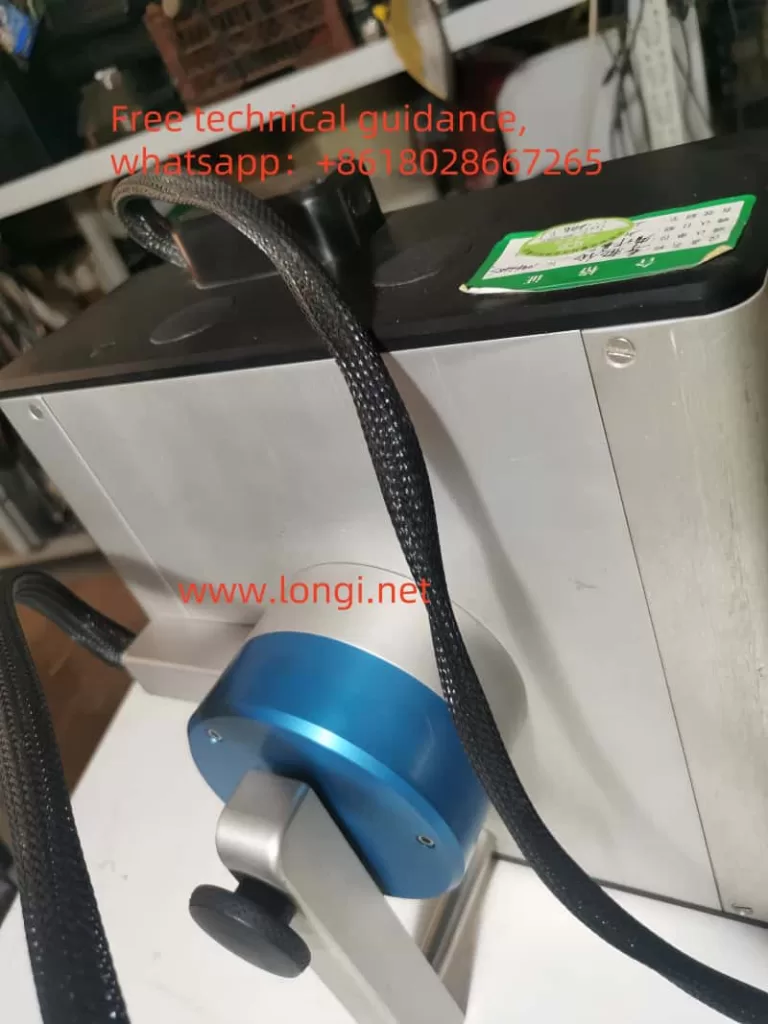
Longi Ectromechanical Company has nearly 30 years of experience in repairing thermal conductivity instruments (including laser thermal conductivity testers, flash thermal conductivity testers, thermal reflectance thermal conductivity testers, and thermal conductivity coefficient testers). We can quickly repair various types of instruments. Additionally, we recycle and sell used thermal conductivity instruments. Please feel free to contact us for more information.