I. Operation Method of the HARS Inverter HS720 Series
The HARS Inverter HS720 Series is a high-performance current vector inverter with a wide range of applications. This article will provide a detailed introduction on how to set the inverter to start via the operation panel and use the panel potentiometer to set the frequency, enabling direct start/stop control via the operation panel and speed regulation through the panel potentiometer.
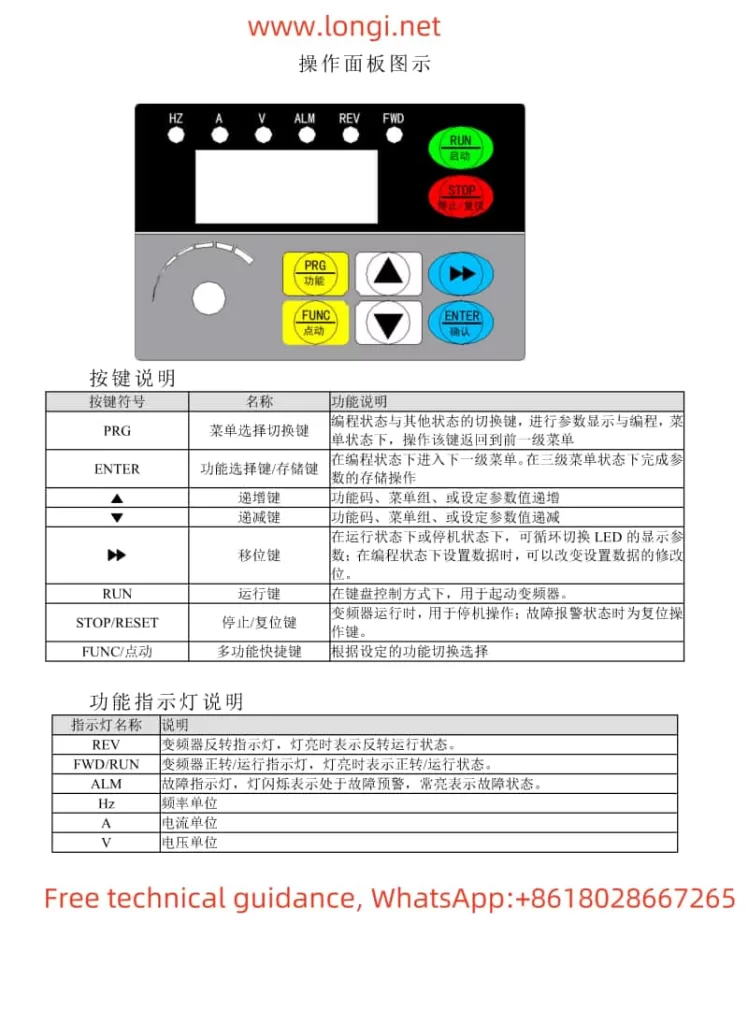
1.1 Setting Operation Panel Startup and Panel Potentiometer Frequency Setting
First, ensure that the inverter’s power supply is correctly connected, and all safety measures are in place. Next, follow these steps to configure the settings:
- Enter Programming Mode: Press the
PRG
key on the inverter’s operation panel to enter the programming menu. - Set Run Command Selection: In the programming menu, find the
F0.02
parameter and set it to0
. This selects the keyboard operation mode for run commands. - Set Main Frequency Source A Selection: Continue to find the
F0.03
parameter and set it to1
. This indicates that the keyboard potentiometer is selected as the frequency setting method. - Save and Exit: After completing the settings, press the
SET
key to save the parameters and press thePRG
key to exit programming mode.
Now, you can start and stop the inverter using the RUN
and STOP/RESET
keys on the operation panel, and adjust the output frequency by rotating the panel potentiometer to achieve speed regulation.
II. Restoring Factory Default Settings for the Inverter
During the use of the inverter, it may be necessary to restore the parameters to their factory default values for reconfiguration or troubleshooting. The HARS Inverter HS720 Series provides a function to restore factory default settings, with the following steps:
- Enter Programming Mode: Press the
PRG
key to enter the programming menu. - Select Data Initialization: Find the
F0.17
parameter and set it to2
. This selects restoring factory default settings (excluding motor parameters and F8 group parameters). - Confirm and Wait: Press the
SET
key to confirm the selection, and the inverter will begin the process of restoring factory default settings. Please wait patiently until initialization is complete. - Exit Programming Mode: After initialization is complete, the inverter will automatically exit programming mode and restore to factory default settings.
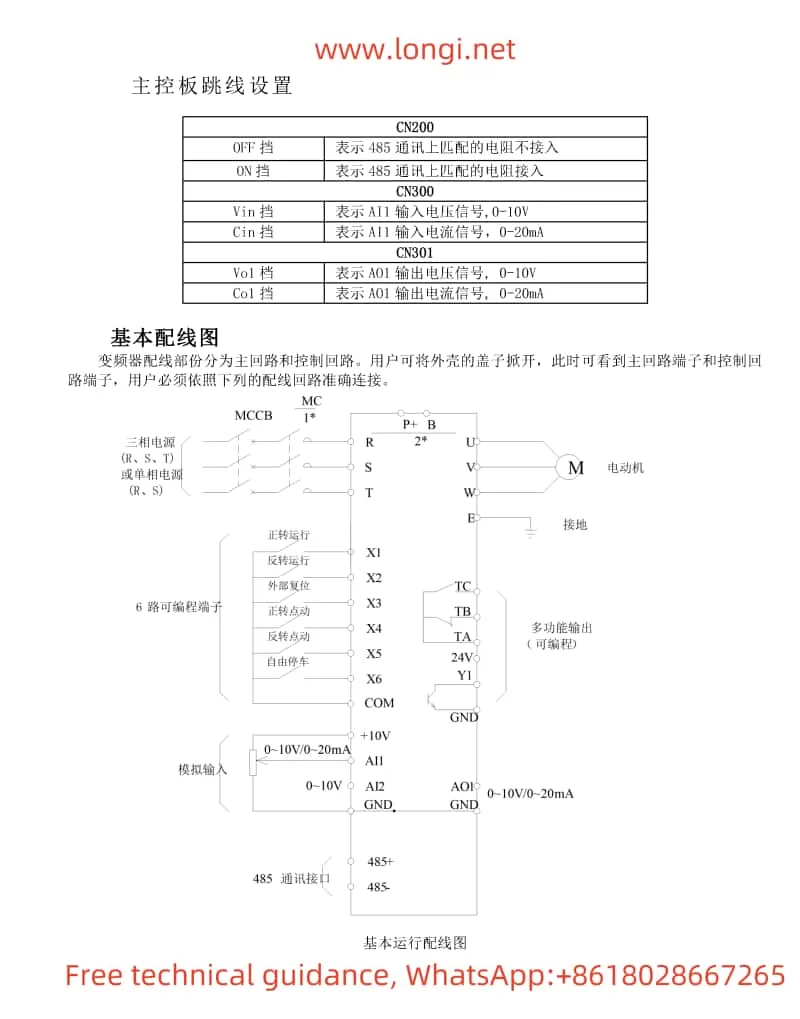
III. PID Control Implementation for a Single Pump
In a constant pressure water supply system, the PID function within the inverter can be used to achieve constant pressure control of the water pump motor. The PID (Proportional-Integral-Derivative) controller is a commonly used feedback control system that continuously adjusts the output signal to make the system output reach and maintain the set value.
3.1 Introduction to PID Principles
The PID controller adjusts the output signal by calculating the deviation between the set value and the actual feedback value, based on three components: proportional (P), integral (I), and derivative (D). Among them:
- Proportional (P): Adjusts the output based on the proportion of the deviation. The larger the deviation, the greater the output adjustment.
- Integral (I): Integrates the deviation to eliminate the system’s static error.
- Derivative (D): Adjusts the output based on the rate of change of the deviation to predict future deviations and make adjustments in advance.
In a constant pressure water supply system, the derivative component is usually not required, so the derivative gain can be set to 0.
3.2 Wiring and Parameter Settings
To achieve constant pressure water supply control using the panel potentiometer as the PID setpoint and port AI1 as the PID feedback value, follow these wiring and parameter setting steps:
Wiring Steps:
- Setpoint Wiring: Connect the output terminal of the panel potentiometer to the AI1 terminal of the inverter (as the PID setpoint input).
- Feedback Wiring: Connect the output signal of the pressure sensor (typically 420mA or 010V) to the AI2 terminal of the inverter (as the PID feedback input).
- Ensure Grounding: Ensure that all signal wires are properly grounded to avoid interference.
Parameter Setting Steps:
- Enter Programming Mode: Press the
PRG
key to enter the programming menu. - Enable PID Function: Find the
FA.00
parameter and set it to1
to enable reverse-acting PID control. - Set PID Setpoint Selection: Set the
FA.01
parameter to1
, indicating that the keyboard potentiometer is selected as the PID setpoint. - Set PID Feedback Selection: Set the
FA.02
parameter to2
, indicating that AI1 is selected as the PID feedback input (Note: This differs slightly from the wiring as AI1 is already used as the setpoint input. In actual operation, ensure that the feedback value is input to the correct terminal, such as AI2). - Adjust PID Parameters: Adjust PID parameters such as
FA.09
(proportional gain),FA.10
(integral time), andFA.11
(derivative time) according to system requirements. In a constant pressure water supply system, the derivative time is typically set to 0. - Save and Exit: After completing the settings, press the
SET
key to save the parameters and press thePRG
key to exit programming mode.
Now, the inverter will automatically adjust the speed of the water pump motor based on the set PID parameters and the feedback signal from the pressure sensor to achieve constant pressure water supply control.
IV. Conclusion
The HARS Inverter HS720 Series is a powerful and easy-to-operate high-performance inverter. Through this article, you have learned how to set it to start via the operation panel and use the panel potentiometer to set the frequency, how to restore factory default settings, and how to use the PID function to achieve constant pressure water supply control for a single pump. In actual applications, you can further adjust and optimize the inverter’s parameter settings according to specific needs to achieve the best control effect.