Danfoss VLT2800 Frequency Converter User Guide
1. Introduction to the Operation Panel
The operation panel of the Danfoss VLT2800 frequency converter is designed to be simple and user-friendly, allowing users to control basic functions and adjust parameters. The key components of the panel are:
- Display Screen: Shows current status, parameter values, fault codes, etc.
- Navigation Keys: Used to navigate between menus and parameters, including arrow keys for up, down, left, and right.
- Operation Keys: Includes keys for start, stop, reset, and other control functions for easy operation.
- Quick Menu Key: Provides quick access to commonly used menus and parameters.
- Change Data Keys: These keys allow users to modify displayed parameters and adjust the operating status of the converter.
With these buttons, users can perform parameter settings, switch operating modes, and monitor the running status of the frequency converter in real-time.
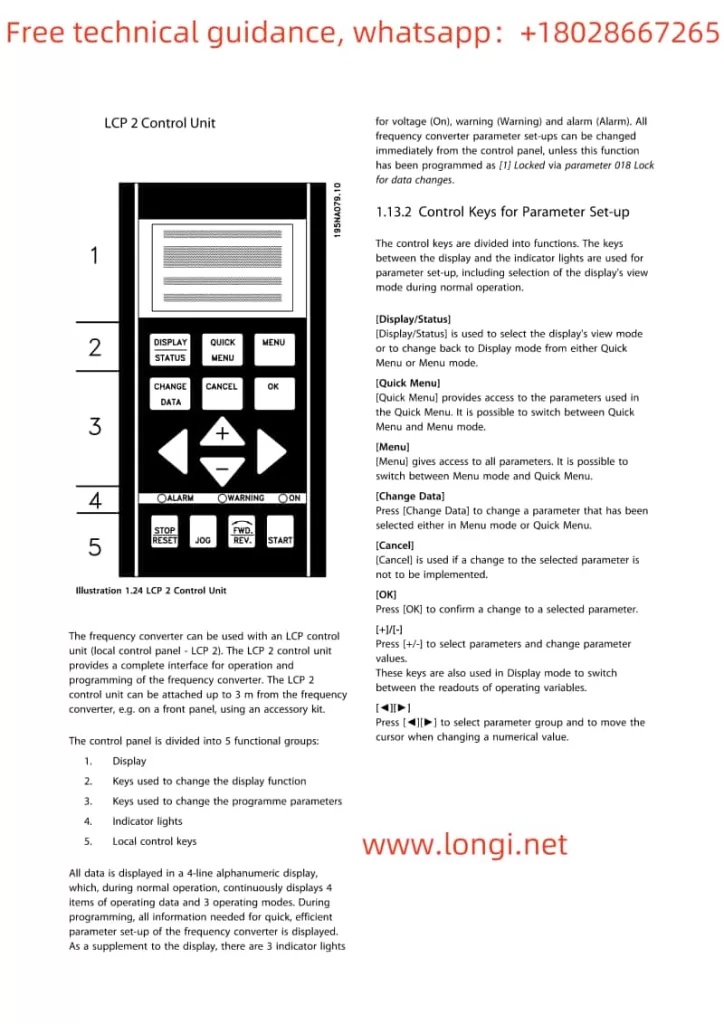
2. Parameter Initialization and Adjustment
When using the VLT2800 frequency converter for the first time or when restoring factory settings, follow these steps for parameter initialization and adjustment:
- Restoring Factory Settings:
- Enter the main menu and select the “Restore Factory Settings” option. The frequency converter will reset all user settings to default parameters.
- Motor Parameter Settings:
Configure the motor parameters through parameter group 102-106:
- 102: Motor Power (PM,N): Set the motor’s rated power.
- 103: Motor Voltage (UM,N): Set the motor’s rated voltage.
- 104: Motor Frequency (fM,N): Set the motor’s rated working frequency.
- 105: Motor Current (IM,N): Set the motor’s rated current.
- 106: Motor Speed (nM,N): Set the motor’s rated speed.
- Speed Control Mode:
- Choose between open-loop or closed-loop speed control to ensure precise control based on application requirements.
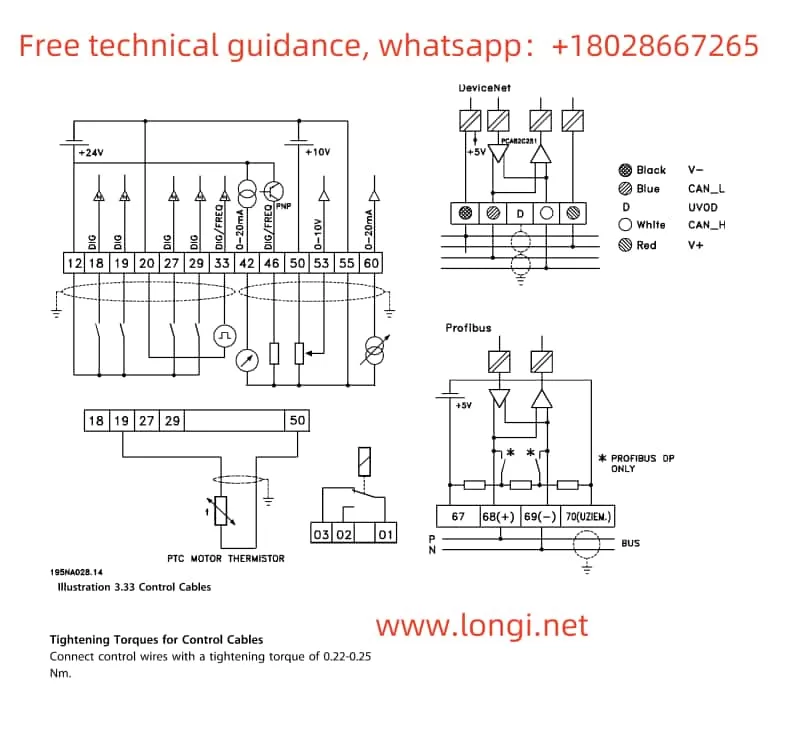
3. Start/Stop Function and External Potentiometer Adjustment
1. Start and Stop Functions via Terminals
The Danfoss VLT2800 frequency converter can be started and stopped using terminal connections. Follow these steps for terminal wiring:
- Start Signal: Connect the start signal to terminals 12 (START) and GND. The converter will start the motor according to the set parameters once the signal is received.
- Stop Signal: Connect the stop signal to terminals 13 (STOP) and GND. The motor will decelerate and stop as per the set deceleration time when the stop signal is triggered.
- Reset Function: Connect an external reset signal to terminal 16 (RESET) to reset the converter when needed.
2. External Potentiometer for Speed Adjustment
To adjust the output frequency using an external potentiometer, follow these wiring steps:
- Potentiometer Wiring:
- Connect the positive terminal of the potentiometer to terminal 55 (+10V output), the negative terminal to terminal 53 (analog input), and ground to GND.
- Parameter Settings:
- In parameter group 300, set the analog input type and configure terminal 53 to be controlled by the external potentiometer.
- Adjust parameters 204 (RefMIN) and 205 (RefMAX) to set the minimum and maximum reference values corresponding to the potentiometer.
By adjusting the potentiometer, the frequency converter’s output frequency can be dynamically controlled, allowing for smooth linear speed regulation from minimum to maximum.
4. Fault Code Analysis and Troubleshooting
The VLT2800 frequency converter features a self-diagnostic function. If a fault occurs during operation, the relevant fault code will be displayed on the control panel. Below are some common fault codes and their solutions:
- E1: Overcurrent Protection
- Cause: Fast motor acceleration, excessive load, or motor short circuit.
- Solution: Check motor wiring, reduce load, or extend the acceleration time.
- E2: Overvoltage Protection
- Cause: Power supply voltage too high or large voltage fluctuations.
- Solution: Check if the power supply voltage is within the specified range, and use a voltage stabilizer if necessary.
- E3: Undervoltage Protection
- Cause: Power supply voltage too low or a sudden voltage drop.
- Solution: Ensure stable power supply and check voltage levels.
- E4: Overheating Protection
- Cause: Poor heat dissipation or high ambient temperature.
- Solution: Check the cooling system of the converter, ensure the fan is working properly, and reduce the environmental temperature or improve ventilation if needed.
- E14: Communication Failure
- Cause: Communication line fault or loss of communication between the controller and the converter.
- Solution: Inspect communication cable connections and reconfigure communication parameters.
By setting the correct parameters, ensuring proper wiring, and accurately identifying fault codes, users can ensure the stable operation of the Danfoss VLT2800 frequency converter and troubleshoot issues as they arise.
This guide provides users with a comprehensive overview of the VLT2800 frequency converter, covering panel operation, parameter setup, terminal functions, and troubleshooting to help them get started and maintain smooth operation of the device.